Things are looking brighter inside Ford Motor Co.’s stamping plant in Hamburg.
The massive Route 5 complex has installed 1,740 LED tandem fixtures that are 70 percent more efficient than the metal-halide light fixtures they replaced. The project was supported by a $1.35 million grant from National Grid, the utility’s largest-ever grant for energy efficiency.
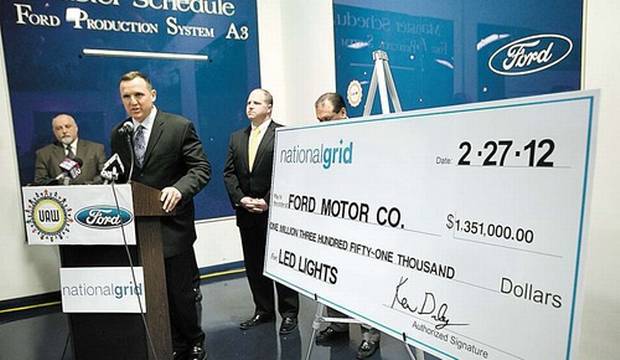
“Something as simple as changing the lighting can contribute benefits not just to the customer but also to the environment,” said Kenneth Daly, National Grid’s president in New York State.
The annual estimated energy reduction from the upgrade — about 10.7 million kilowatt hours — is equivalent to the amount of electricity used by 1,400 homes in a year, Daly said.
The project’s value was $2.7 million. Ford and National Grid officials hailed the results at a Monday news conference at the plant, which stamps parts for vehicles including the Ford Edge and Flex.
Daly said the project reflects National Grid’s goals of investing in the electric infrastructure, helping keep customers’ energy bills down, and giving back to its community.
A Lancaster company, S3J Electronics, manufactured the lighting units. They were installed by Ford hourly workers, represented by the United Auto Workers, and salaried employees. “They did it within time. They did it within budget. They did an outstanding job,” said David Buzo, the plant manager.
The fixtures were designed specifically for the Ford project, said Adam J. Metz, S3J’s president. “Extra steps were taken by our engineering staff to ensure these lights would work in the highest temperatures of the plant and provide even and consistent lighting,” he said.
Buzo praised the results: “It’s great lighting. It kind of surrounds you, kind of engulfs you, and it gives you a clear picture of what you’re working around as far as your surroundings.”
The light fixtures are rated to last seven to 10 years, operating 24 hours a day, seven days a week, Metz said. Their staying power should reduce operating costs and limit how often workers need to tend to the lights, which are 45 feet above the production floor.
The quality of the light is also an improvement, Metz said. “The color rendering of these lights makes it a safer work environment by providing truer colors to the workers’ eyes, as well as allowing workers to differentiate between colors easier,” he said.
The lights provide better output than the fixtures they replaced, despite using less energy, Metz said.