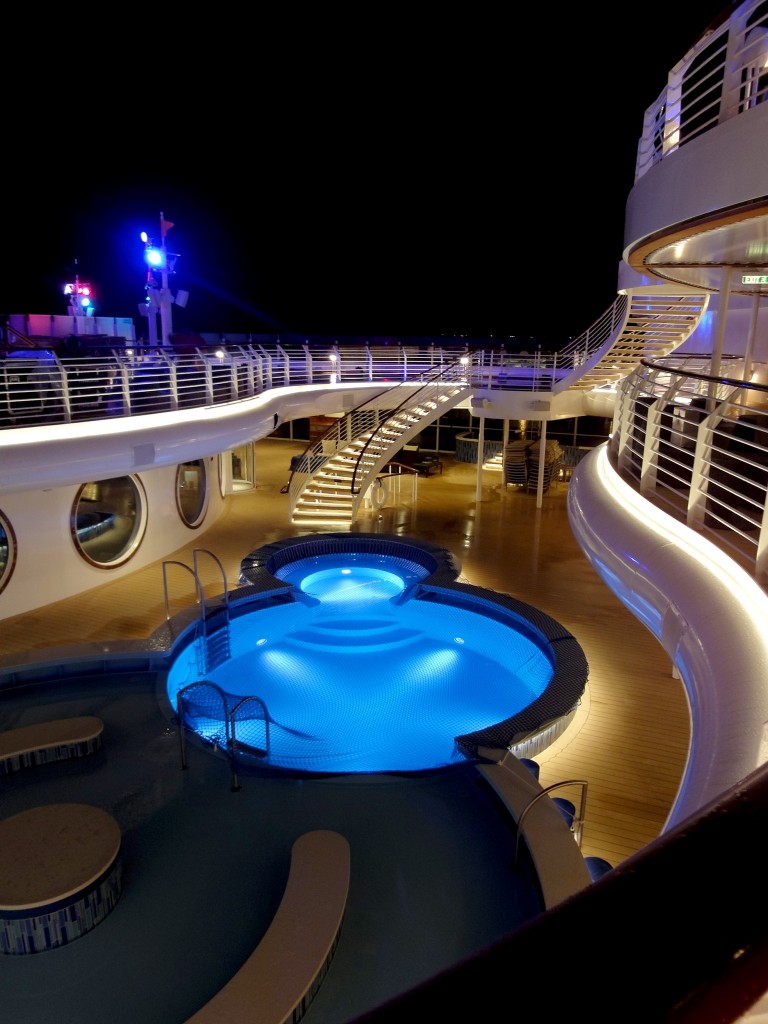
Ulrike Birnbaum has designed for brands including Jaguar, Landrover, Disney, British Telecom, Bodyshop, Vapiano, Christie's Auction House, Bloomberg, Seabourne, Steiner Spa and many more. Having lived in Berlin, Amsterdam, London and New York, she gained experiences as an architectural lighting designer in the world of opera, cruise ship and show lighting. Before founding CONTINUUM STUDIOS, she worked for the 'English National Opera', and later joined 'ARUP' as a senior lighting designer.She was also previously the principal architectural lighting designer for Imagination Ltd. and worked for MRD in New York. Her decision to establish a company for architectural lighting design with studios in New York ,U.S. and Munich,Germany, brought together highly skilled lighting designers with various backgrounds, such as film, opera, product design, textile & material design, electrical engineering, 3D animation, graphic design and digital art. We interviewed Ulrike Birnbaum about her personal experiences with LED light fixtures in architectural lighting design.

-
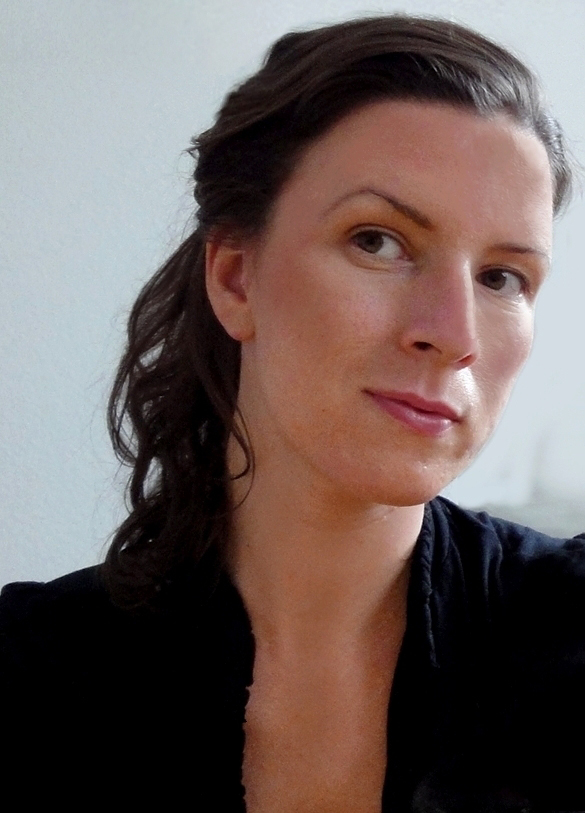
-
Ulrike R. Birnbaum, architectural lighting designer and founder of Continuum Studios.
Photo Credit: Ulrike R.Birnbaum
How did you get involved in LED luminaire design?
Actually, I had no idea I would get into designing LED light fixtures. Luminaire design discovered me. There was no aha-moment as such. I studied 'Interior Architecture' first, gained experiences as an interior architect, decided then to study 'Architectural Lighting Design' and eventually worked all over the world in the field of lighting. However, it was during my interior design studies when I discovered lighting design is a complex design field that requires specific sensitivity and knowledge about how light works, what it does with the human perception and what the technical challenges are that we face in the lighting industry, an industry that moves very slowly from 'quantity to quality'. Especially when it came to the topic of LED fixtures: Surely, the lighting market is swamped with light fixtures that work like a toolbox consisting of housing, LED chip and a range of lenses. The user is encouraged to apply the 'plug-and-play' principle, but this will only give you a poor imitation of what the fixture's potential is like. Quality light fixtures with particular requirements are always developed of components that are carefully geared to each other. The lighting designer should be the one who defines the luminaire's needs and its relevance for the project, and not the off-the-shelf fixture. As an architectural lighting designer, I always had a clear understanding and idea of the fixture required to achieve high-end lighting design. I naturally got into designing luminaires with customization far from standard lighting solutions. LED is not just another light source. It's a component that has to be integrated into a system that is well though-out. It's no longer a ‘new lamp in an old box' mentality, you have to redesign your product.
-
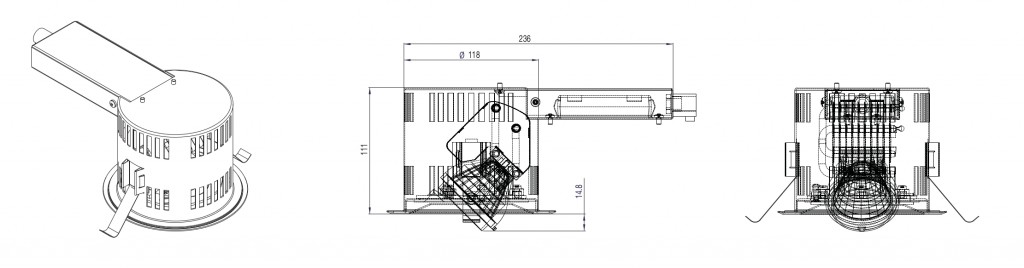
-
Downlight Design Image
Photo:Continuum Studios
Photo Credit: Ulrike R.Birnbaum
So, apart from the question of technical high-end quality and required bespoke lighting solutions, how do you start the light fixtures design process?
The great thing about our team at Continuum Studios is every designer is always interested about how light can make a difference. Everyone contributes to that 'question' with another strategy or idea: What is the story that can be told about or in a venue? What lighting approach enables us to create a distinctive look and feel? We design luminaires to develop signature styles or brand identity looks. It's basically about having a solid idea and concept to improve the space's look and feel, so when a client or architect questions it, you have the answer.
Established standard lighting solutions, such as regular patterns of downlights spread out the ceiling are defined by emotionless calculation that don't fit into our design philosophy. We think beyond the outer shell of the fixture, it’s not just the look of the housing since the light performance of the luminaire is of major importance. Light performance defines the atmosphere in a venue. One can witness the importance of matching the lighting concept to space easily. The most beautiful architecture interior can be destroyed by poor lighting. Have you ever had the experience of restaurants that are beautiful at daytime, but you wouldn't consider having dinner there in the evening?
Do you remember the first LED light fixture that you designed?
-
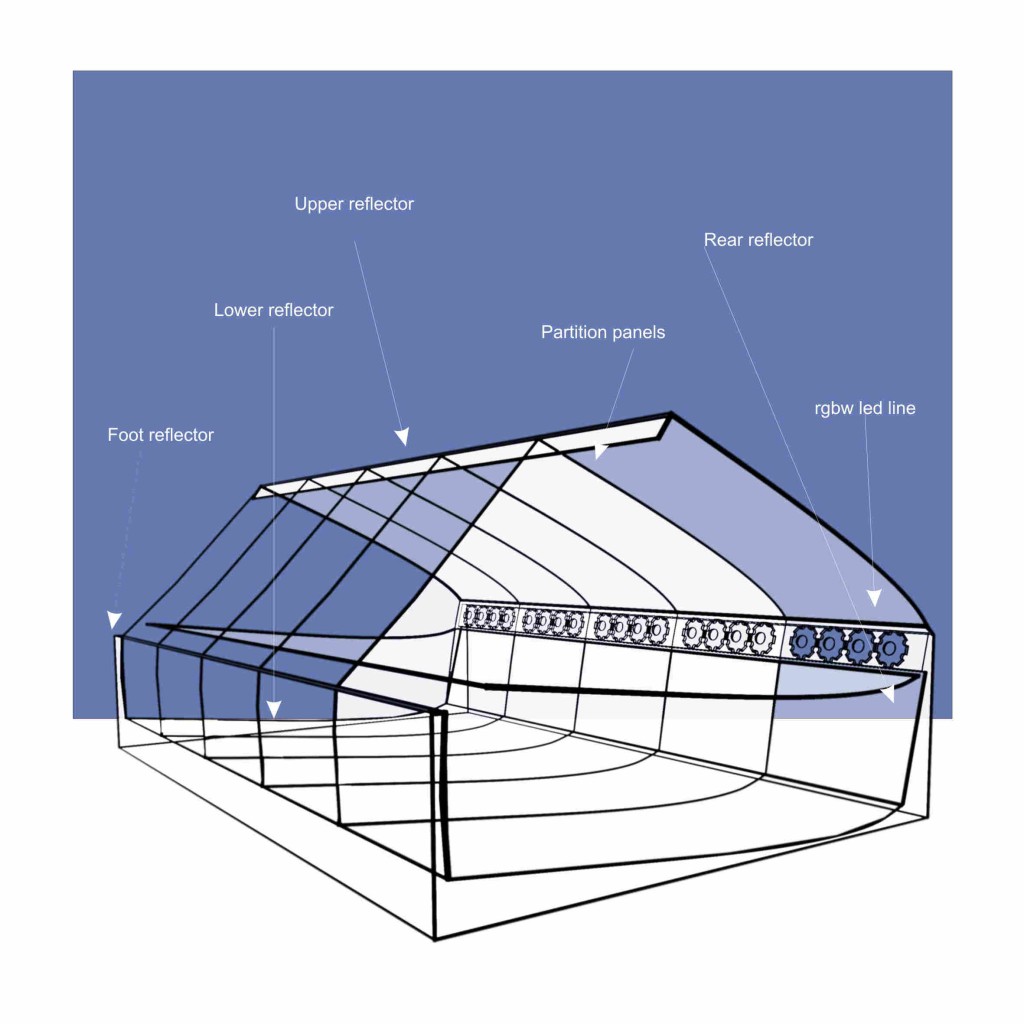
-
CS-ENO Reflector 1
Photo: Continuum Studios
Photo Credit: Ulrike R.Birnbaum
Well …during my work as an interior architect I already designed a few luminaires. But these were merely decorative fixtures, and we designed ample LED fixture prototypes by trial and error during my masters program in architectural lighting. But the first carefully calculated and designed architectural LED fixture was the one for the English National Opera. It involved a lot of study and experimentation. I developed this luminaire in close cooperation with Kevin Sleep, 'Head of Lighting' at the Coliseum. There was no luminaire at the time that would work like a followspot, while avoiding scattered light around the actor on stage. I developed a RGBW LED fixture to be positioned on the stage's front edge, which dynamically adjusted the beam’s vertical light angle, horizontal position on stage and hue according to the movement of the actor. Even though this was hard work, we had fun creating something entirely new in the world of LEDs.
-
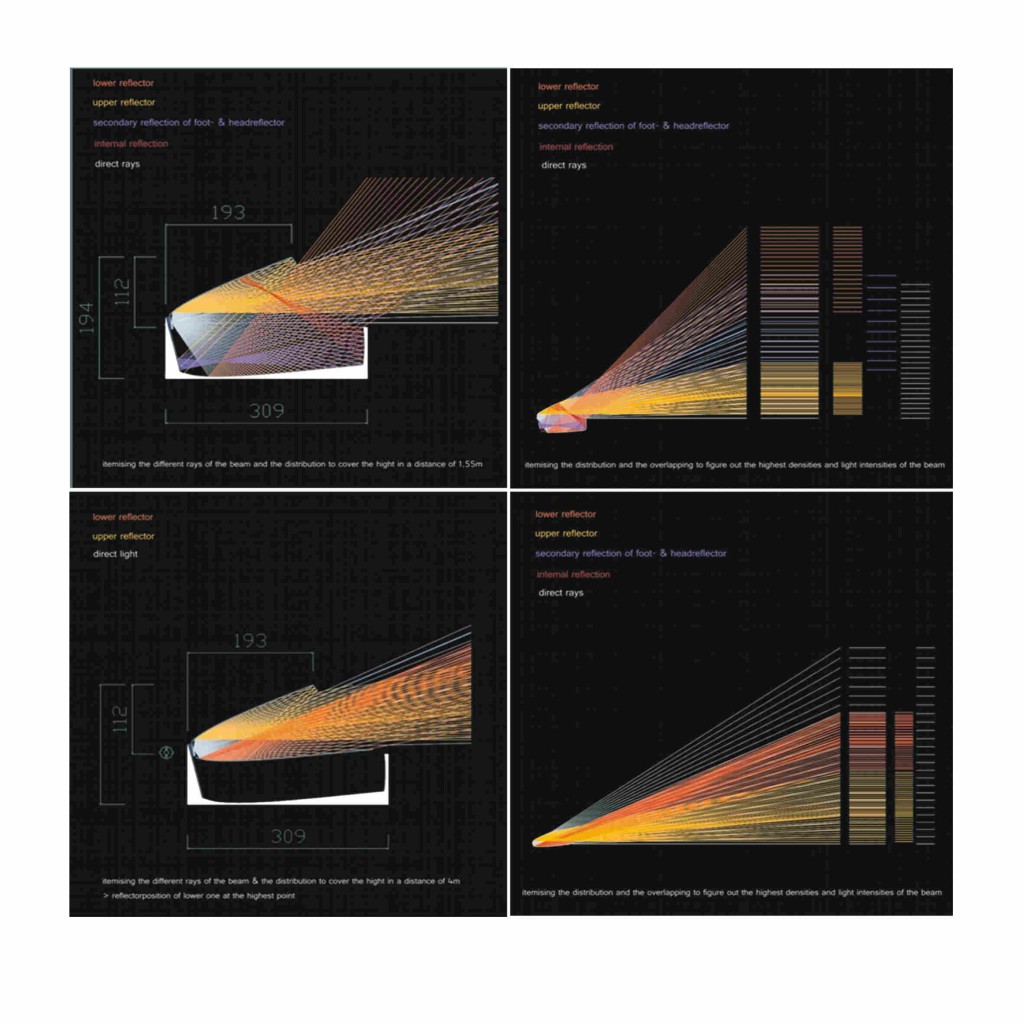
-
CS-ENO Reflector 2
Photo: Continuum Studios
Photo Credit: Ulrike R.Birnbaum
Did this fixture go into mass production?
Not this one. But one of my most successful LED fixture designs, the LED downlight I developed in cooperation with Cooper Lighting for Walt Disney's Cruise Liners 'Dream' and 'Fantasy' did. I was the principal architectural lighting designer on the project and keen on a high-end lighting approach. This of course demanded for a custom tailored light fixture, due to the facts we had to bear in mind in such naval projects.
-
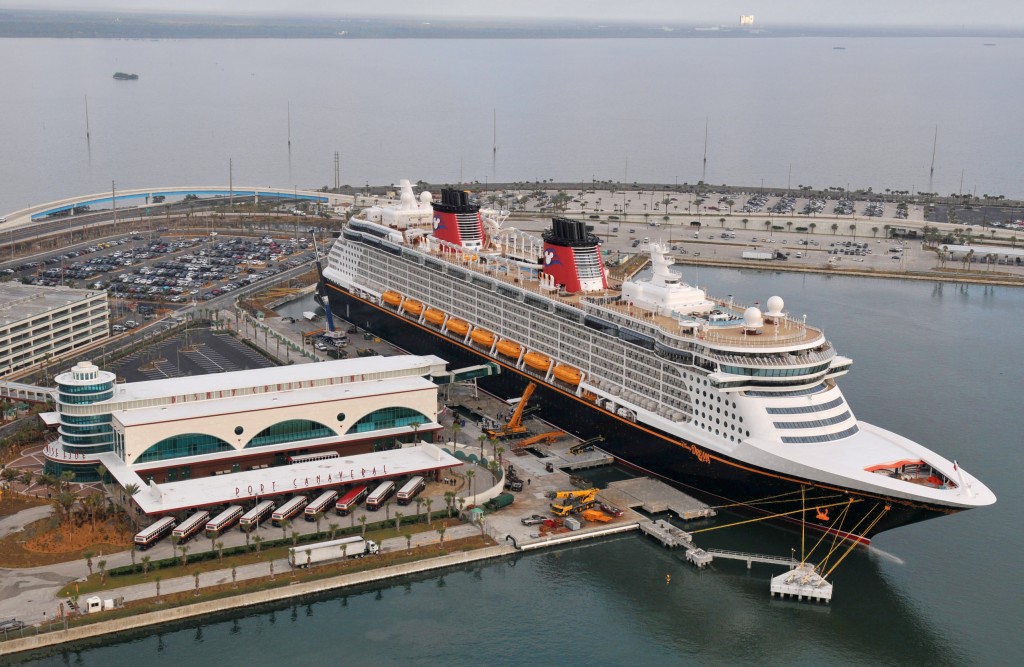
-
Photo: Cruise Liner "Dream"
Project: Disney Cruise Line - Disney Dream & Fantasy
Photographer: Phelan Ebenhack
Owner: The Walt DIsney Company
Builder: Meyer Werft
Was that a special request from the ship-owner or shipyard? Tell us more about the LED fixture that you developed for the cruise ships. How did you approach the "naval project"?
The energy efficiency of the lighting system on the ships was a big question. The total energy that's used on such a vessel is considerable. Just think of how LED technology alone can pare down the power and fuel used to illuminate a ship to a minimum! Still, the luxurious and unique interior illumination of the cruise liner was most important to the client, and so was the vessel's external presence in the evening.
In terms of sensibility and responsibility for such a large scale project, we did a ton of research on existing cruise ships to learn from their problems. We spoke to owners of the cruise ships we visited, and also to hotel directors, restaurant managers, electrical engineers and technicians on board.
It is interesting when you are on board and look around. When ships are designed, they tend to mainly use Compact Fluorescent Light (CFL) fixtures, which we were told to keep total power consumption to a minimum. Drawback number one is certainly the poor Color Rendering Index (CRI) of CFLs. Especially in the retail areas and restaurants, where you want your food to look rich in color, fresh and healthy; you certainly wouldn't want to see a greenish tinge on your steak. The second reason to rule out CFL fixtures is the housing. They are large in size compared to halogen or LED downlights and quite obtrusive on low ceilings. It is impossible to direct a crisp light beam in a pre-defined angle to a certain position in a room, there is no adjustability. It will always just be a wash light and isn't appropriate to work out the venue's theme or story.
-
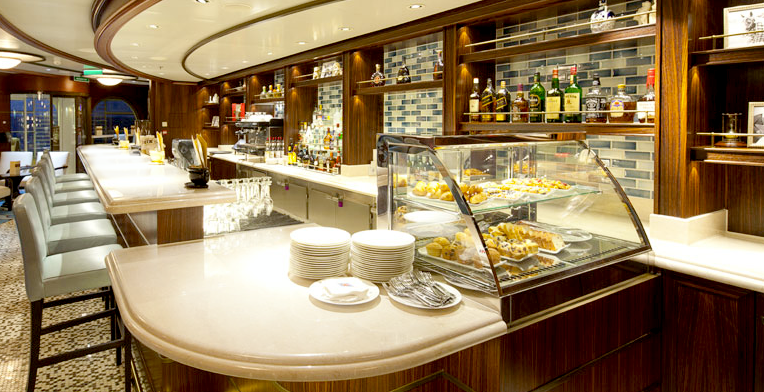
-
Photo: Interior - Café Bar- Disney Dream
Project: Disney Cruise Line - Disney Dream & Fantasy
Photo Credit: DCL
Owner: The Walt DIsney Company
Builder: Meyer Werft
We found low voltage halogen sources in places where CFL wasn't installed. These are indeed adjustable and halogen bulbs are available in various beam angles, but that's where the ship's electrical team faced increasing maintenance issues. There was no available documentation on beam angles used in the initial design. Consequently a standard halogen bulb with flood light characteristics was used to replace broken light sources. Since none of the fixtures were lockable in position, the light focus would alter with the maintenance procedures over the years, and due to constant vibration from the vessels' machinery. You could tell from just visiting public areas on the ships, the lighting look of the venues must have changed drastically over the years. Where a spotlight with a tight narrow beam was needed, we found a spot with flood light characteristics instead. The beam spread all around, but didn't hit the niche where the light spot should have been focused onto.
In my opinion, there is nothing worse than returning to a project one or two years after completion and see it under maintenance. Our aim was to prevent that from happening. On such a ship there is a total of more than 2,000 downlights just for ambient lighting in public spaces. We needed a large scale project solution. We were looking for a lighting technology unit that could deliver something unique across the scale of the project, reliable, with various beam angles, high CRI, consistent brightness, easy to maintain, long lifetime and a reporting system that would facilitate ease of maintenance. Most important was to find a luminaire that guarantees the project would look just as good in five or 10 years from now. Given that starting position and hard facts, LED seemed to be a reasonable solution. We reviewed the products of numerous manufacturers at that time, but didn't find what we were looking for, which sparked our studies on a possible customized solution.
-
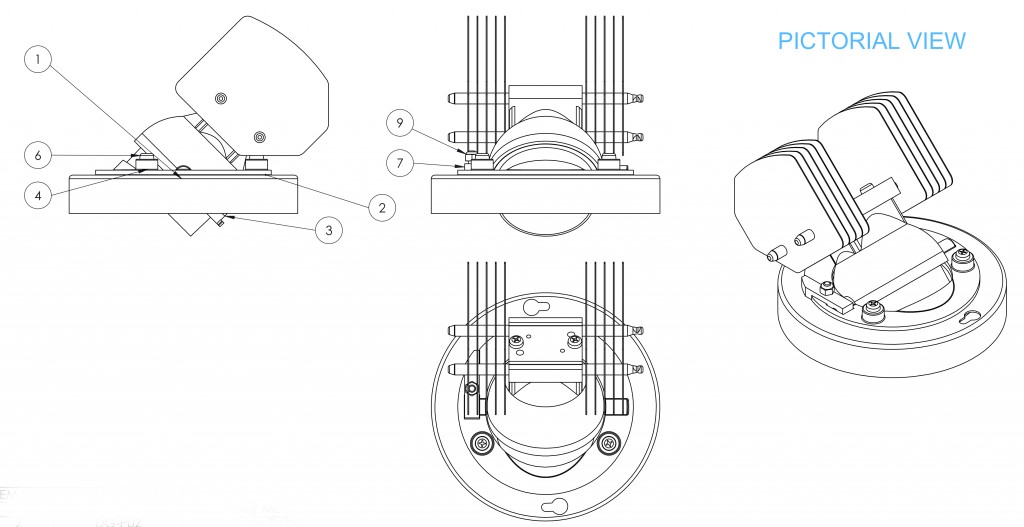
-
Downlight Design 2
Photo: Continuum Studios
Photo Credit: Ulrike R.Birnbaum
So, the target was to develop a lock-type LED fixture with the ability of rotation and tilt and the possibility to exchange optical lenses?
I didn't like the idea of using optics. After many tests in our studio, I came to the conclusion that light loss of a LED fixture using lenses was by far too high, in comparison to the combination of a LED with reflector. The challenge we had to surmount was to find the right multichip LED for an exchangeable reflector system to provide three different beam angles from one luminaire family. To keep the fixture size as small as possible, a huge proportion of time was spent on the development and optimization of the reflectors and their facet structure. It involved a lot more study and experimentation. One of the things we strove to achieve was to avoid visible LED chips in the light fixture. For a high-end lighting design, we didn't want to draw people's attention to the light fixtures. We wanted them to enjoy the lighting and the atmosphere in the venues. The light fixtures were meant to merge with the interior design and give a classic look. We felt that this would be needed for the beautifully designed interiors on the new cruise ships 'Dream' and 'Fantasy".
-
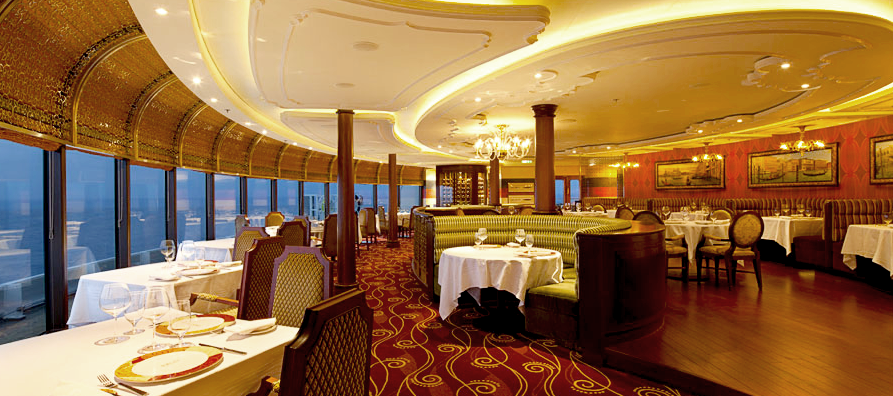
-
Photo: Interior - Italian Restaurant - Disney Dream 1
Project: Disney Cruise Line - Disney Dream & Fantasy
Photo Credit: DCL
Owner: The Walt DIsney Company
Builder: Meyer Werft
Multichip LEDs were quite new on the market at the time. I decided to experiment with chips of various well-known manufacturers and tested them for heat development, light color consistency, color temperature and CRI.
CRI was an interesting series of tests. After receiving measurement results of the spectral distribution, I tested the LEDs dishes. I used plates with all kinds of fruit, meat, fish, pasta - food in all colors and textures to find out how well and correct the food's color would be perceived under each LED light source. These tests were crucial to guarantee the perfect performance of the prospective LED fixture in the ship's restaurants.Since I planned to cover as much space possible with the newly developed LED fixture family; I continued the series of tests on textiles and various materials in different colors. The results and inequalities were striking and limited the choice of LED chips to a small range.
The third component to take care of was housing. We had to ensure the fixture would sit tight in the ceiling cut-out, without making any rattling noises due to the ship’s vibration. The tilt and pivot had to be locked to keep the light beam in position to the defined focus we set up. Bearing in mind that we didn't want any visible screws or locking bolts, the trim ring would have to be easily installed and fixed.
After all these tests and investigations, I knew precisely what I wanted to create with a luminaire manufacturer, and what we could achieve together. My target was to try and keep one family of products with features including ease of communication, ease of control, product maintenance and talk back system. I also felt it would be much easier to have one manufacturer responsible for the huge quantity of light fixtures for the vessels.
The specialist I brought in was Rod Dixon, who worked for Cooper Lighting at the time. He was specialized in the calculation and development of reflectors and had immense experience with multichip LEDs. It was a rewarding collaboration, given his skills in combination with my precise concept gained through the studies.
Meaning you ended up with a fixture family?
Actually … yes. As a result of the collaboration with Rod, we were able to design a LED fixture family with the same housing dimension and shape for all light fixtures.
-
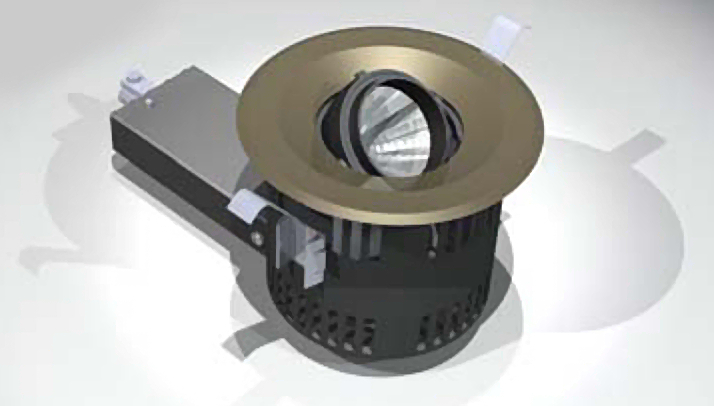
-
Downlight Image 1
Photo Credit: Ulrike R.Birnbaum
We managed to keep the diameter to a minimum size of 120 mm and the trim ring to 135mm. Advantages of the redesigned heat sink is the height of the fixtures did not exceed 115mm, with 35 degree tilt and 360 degree rotation. We reached the physical limits that such a small size gimbals would grant us. One of Citizen's multichip LEDs was chosen as the light source in warm white and neutral white, and dimmable with PWM. The reflectors we developed emitted light beams in 12 degrees for highlights and in 24 degrees to enhance textures and define certain areas or walk ways. For general lighting, 40 degrees was used for even light distribution. To hide visible screws, a magnetic trim ring was designed and built. The fixture's position is fastened below the focus and covered with the magnetic trim ring that sits underneath the locking bolt.
The combination of fixture types out of that luminaire family allowed for various lighting scenarios. For example, in corridors and staircases without daylight, I used the 40degree fixture in neutral white and combined this scattered light beam with a crisp narrow beam of 12degree in warm white in the ship's center. This gives passengers the impression of natural daylight, the scattered general lighting is similar to sunlight, and the directional warm narrow spotlight assimilates sun rays.
-
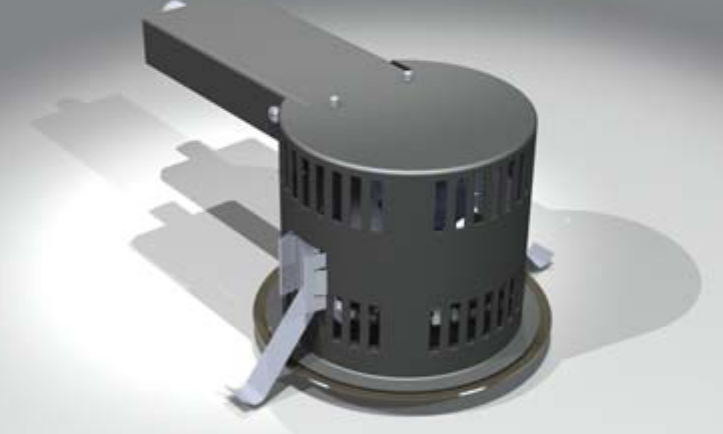
-
Downlight Image 2
Photo Credit: Ulrike R.Birnbaum
How was the client, shipyard and passengers reaction, since this is an entirely new approach to cruise ship lighting?
All the experiments, meticulous studies, calculations, tests and hand samples convinced the client, shipyard and interior designers at last, that LED technology was the right way to go.
A big success was the reaction of people that didn't know we implemented LED technology. It seemed impossible to see the difference between a halogen source and LED fixture. People kept asking us, how we got rid of the heat load in spaces, since they couldn't believe that it was an LED light source and not halogen. Indeed, the quality of the LED fixtures gimbals met the highest quality expectations.
The total LED units per ship is about 2500 luminaires for public interior areas, and excludes staterooms, exterior and crew areas.
-
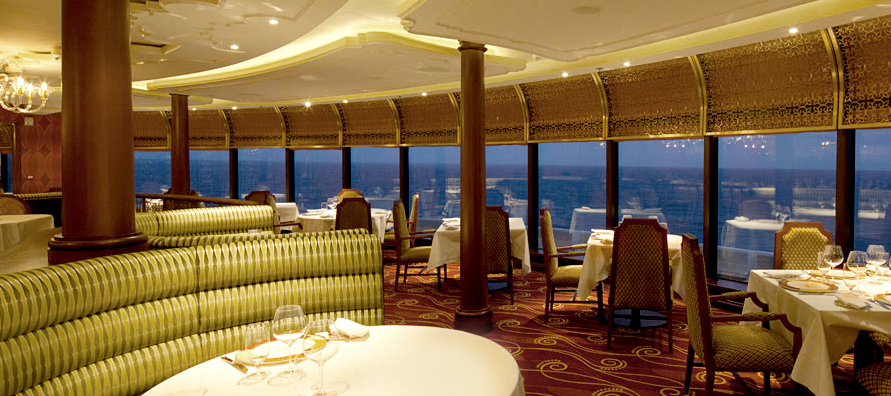
-
Photo: Interior - Italian Restaurant - Disney Dream 2
Project: Disney Cruise Line - Disney Dream & Fantasy
Photo Credit: DCL
Owner: The Walt DIsney Company
Builder: Meyer Werft
The cruise liners 'Dream' and 'Fantasy' were the first passenger ships worldwide that used LED as the main light source. Up to 80% of all fixtures on board were covered by LED technology.
The clients love what they have and are very proud of the ship's prominence and style that we achieved with our LED lighting concept.
Does your team at Continuum Studios have more LED projects like this in the pipeline?
We do. There is a current project where we try to keep all ceilings clear of any light fixtures, since they are made of fair-faced concrete. No holds barred, but don't touch the ceilings. This was an entirely new challenge that pushed the limits of architectural lighting design. Our team keeps thinking about new ideas that we could develop together with the lighting industry. We want to go beyond the standard. We really try to use LEDs as the tool for unconventional lighting solutions and want to get away from 'standard solutions' that are in danger of being 'put onto the architecture' without being integrated and designed to enhance architecture. We love systems that are well thought outs for architectural environment and for our clients.
-
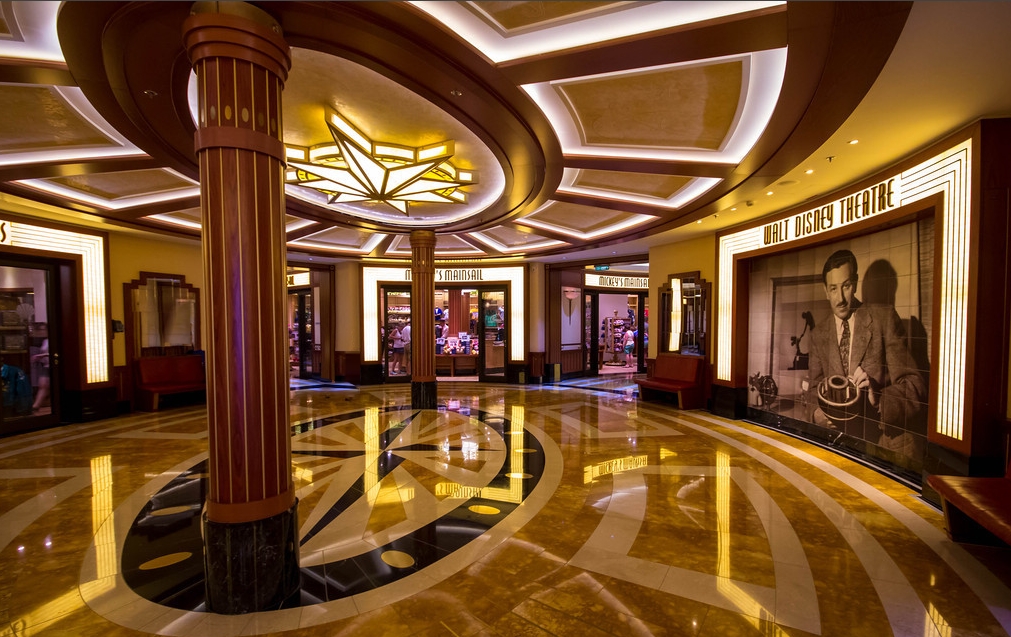
-
Photo: Lobby retail area on Disney Cruise
Photo Credit: DCL
Owner: The Walt DIsney Company
Builder: Meyer Werft
-
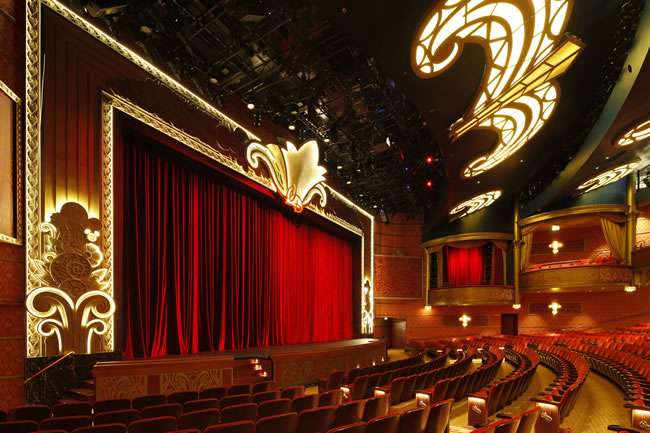
-
Photo: Theatre stage on Disney Cruise
Photo Credit: DCL
Owner: The Walt DIsney Company
Builder: Meyer Werft