Price competitions are affecting almost every aspect of the LED industry, and are observed in manufacturers chip technology developments, such as the emergence of Chip Scale Package (CSP) LEDs.
“The essence of CSP technology is to make the smallest LED chip possible, but are the smallest chips really the most cost effective and offer the best lumen (output)?” questioned Harrison Lin, Senior Director of R&D Division, CSP Project, Everlight at LEDforum 2014 in Taipei, Taiwan on Oct. 30, 2014. “Manufacturer's creation of smaller LED chips is predominately to costdown.”
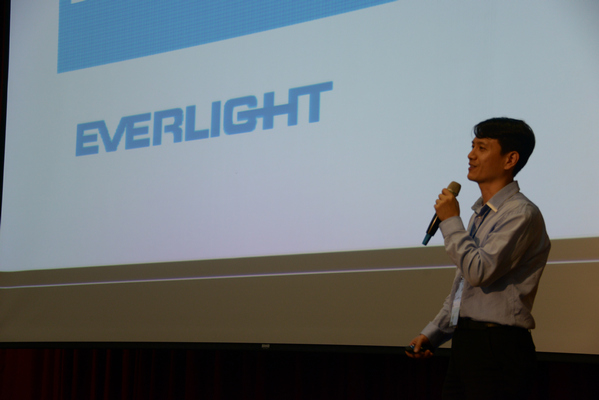 |
Harrison Lin, Senior Director of R&D Division, CSP Project, Everlight starts off his presentation with a joke at LEDforum 2014. (LEDinside) |
Japanese electronics manufacturer Mitsubishi was the first to launch CSP package in 1994. There are still several definitions on the market for CSP. The Electronics Industries Association of Japan defines CSP as the ratio of the chip area and package size greater than 80% of the package, while J-STK-012 standard DoD Component Supply center defines CSP as an area less than 120% of Large Scale Integration (LSI) package. Panasonic defines CSP as the side length of LSI packages difference packaged chip edge length and less than 1mm of products. “Panasonic’s definition is a bit strange, and not suitable for the LED industry,” said Lin.
Originally used in computer chip packaging, CSP package methods in the LED industry include substrate and non-substrate. Substrate materials consist of ceramic (aluminum oxide or aluminum nitride based), metal-core printed circuit boards (MCPCB), or flat PLCC LF. The use of substrates can affect the spacing required between chip components during the surface-mounting device (SMD) production phase.
“In general, most SMD manufacturers will space (the LED chips) between 150-200 mi,” explained Lin. “If the LED chip size and spacing is too small, manufacturers will actually experience some difficulties during the SMD phase.” Hence, smaller LED chip sizes are not always cost effective.
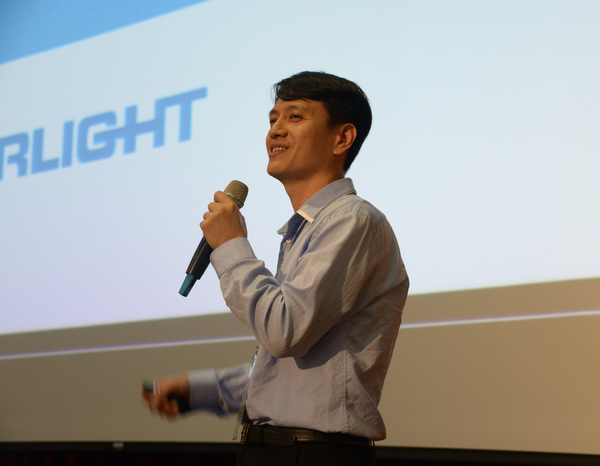 |
Harrison Lin, Senior Director of R&D Division, CSP Project, Everlight changes powerpoint slides during his presentation. (LEDinside) |
In traditional non-directional LED light sources, earlier chip packaging technologies were more costly, offering lower luminous output and lumens per dollar (lm/$). Current EMC or SMC package technologies provide 1,500-2,000 lm/$. Chip on Board (COB) solutions also follow a similar logic of providing smaller and more cost effective light sources. The advantages of COB include more uniform light distribution.
As for the popular flip-chip, Lin highlighted the chips offer better thermal dissipation, luminous flux, and gives manufacturers freedom to redesign chips. The chip’s light reflection side, the position of the PN-junction can also be relocated, as well as its isolation. “Flip-chips are a better solution in high power operations, since it can use higher electric current drives in a same area, resulting in higher lumens output,” explained Lin. Other well-known advantages of flip chip is it lowers EMC package costs by removing the need for lead frames and wire bonding.
A comparison between an EMC packaged LED and CSP LED reveals the former has more advantages in light output and brightness. The EMC package LED has a light output of 120 lm, lighting area of 7 millimeter square, light density of 120. In comparison a CSP LED has a light output of 105 lumens, lighting area is also smaller at 1.21 mm2, and light density of 86.78.
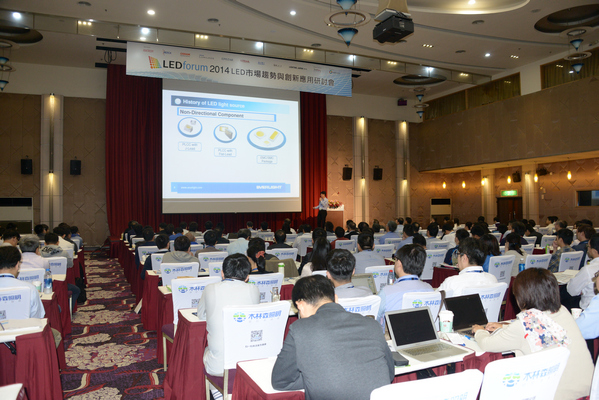 |
Attendees take notes while Harrison Lin, Senior Director of R&D Division, CSP Project, Everlight delivers his presentation. (LEDinside) |
CSP LED applications include smartphone flash LED, backlight, lighting, and in filament LED bulbs. There are many CSP LED on the market including those manufactured by Philips Lumileds, Cree, Samsung, Seoul Semiconductor and Toshiba. Toshiba’s CSP chips is slightly different from others since it uses GaN-on-Si material.
Taiwanese LED manufacturer Everlight’s CSP luminous flux will reach 120 lm in 4Q14 under a 600 mA driving current, and have a forward voltage of 3.35 volts (v). The company aims to eventually raise CSP luminous flux to 133 lm, while driving down forward voltage to 3.26 v. within one year. The ultimate goal, though, is to scale up luminous flux to 138 lm. The company also aims to eventually expand its ESD Protection CSP LED series by launching the new ESD Protection HBM 8KV during first quarter of 2015, said Lin.
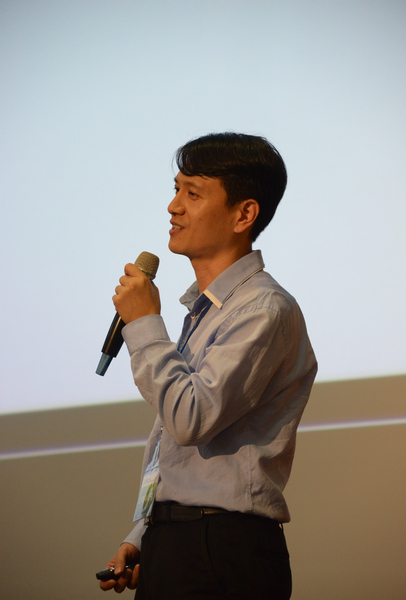 |
Harrison Lin, Senior Director of R&D Division, CSP Project, Everlight. (LEDinside) |
(Author: Judy Lin, Chief Editor, LEDinside)