Photolithography for the manufacture of liquid crystal displays (LCDs), semiconductors, and printed circuit boards (PCBs) is another major application for mercury lamps classified under item 4(f) in the exemption list of the RoHS Directive, in addition to curing, which was described in the previous post.
Photolithography is a lithography process in which a substrate coated with resist is exposed to light or an electron beam to draw a designed circuit, and high-pressure mercury short arc lamps are mainly used as its light source.
High-pressure mercury short arc lamps contain mercury, an environmental pollutant. LEDs are expected to be used as an alternative technology. However, it is not easy for LEDs to produce the radiant flux required for photolithography and be equivalent to high-pressure mercury short arc lamps. Therefore, in the RoHS Directive, the manufacture and sale of high-pressure mercury short arc lamps are allowed under the exemption until at least February 24, 2027, because no alternative technology has been established.
In addition to containing mercury, high-pressure mercury short arc lamps have several other practical problems when used in photolithography applications. First, it takes a few minutes to light up after the switch is turned on, making it not possible to have on-off control. This means that the switch must be left on constantly when the photolithography device is in operation. Furthermore, the lifetime of high-pressure mercury short arc lamps is only about 1,000 hours. If the lamps are used beyond their lifetime, they may become damaged and there is a risk that mercury is exposed. Therefore, they usually need to be replaced after about 2 or 3 months. It also requires a special power supply control that applies an overcurrent to turn on the light and then lowers the current to a stable current to continue applying current, requiring a ballast for that purpose.
LEDs are expected to be an alternative technology that can not only contribute to making these applications mercury-free but also solve all these problems at once.
High-pressure Mercury Short Arc Lamps for Photolithography Applications → LED Adoption Case Studies
As explained above, there are several applications for photolithography using high-pressure mercury short arc lamps, including the manufacture of semiconductors, and printed circuit boards (PCBs). This post will introduce an actual case study of LED adoption for photolithography of LCDs.
In the photolithography of LCDs, ultraviolet rays emitted from a light source are spread by an optical system to expose a large-area object. In this process, the size of the light source is pre-determined to some extent because the optical system is designed to match the size of the object. While UV LEDs could be arranged within this designated area, in the past, the number of LEDs that could fit in the designated area was not sufficient to produce enough radiation flux. However, the efficiency of UV LEDs has dramatically improved in recent years, so that even with the same number of LEDs, it is now possible meet the radiation flux required to expose an object, enabling photolithography to finally have an equivalent to that of high-pressure mercury short arc lamps. The increased efficiency has also solved the problem with the heat dissipation design, enabling the adoption of LEDs and their introduction to manufacturing sites ahead of other applications.
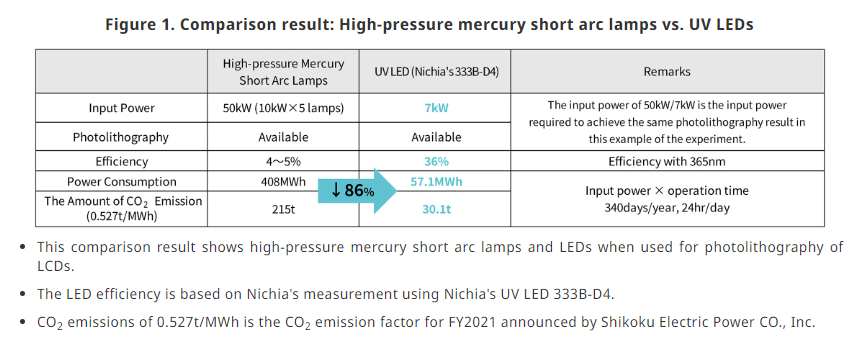
In addition to meeting the initial goal of mercury-free by achieving equivalent photolithography as an alternative technology, LEDs can also reduce power consumption and CO2 emissions because their efficiency is much higher than that of high-pressure mercury short arc lamps. The required input power to achieve the same photolithography result is 50kW for high-pressure mercury short arc lamps for one standard photolithography device, whereas LEDs are 7kW. Assuming that both lamps are operated 24 hours a day for 340 days, the annual electricity consumption of high-pressure mercury short arc lamps is 408MWh, while that of LEDs is 57.1MWh. Even without taking into account that the LEDs can be quickly turned on and off, 86% can be saved.
CO2 emissions can also be calculated based on a CO2 emission rate of 0.527 tons per MWh of electricity consumption. The amount of CO2 emission by high-pressure mercury short arc lamps is 215t, while the amount of CO2 emission by LEDs is 30.1t, achieving a similar reduction of 86%.
Furthermore, LEDs have excellent electrical responsiveness, eliminating the need for ballasts and reducing the input power, making it possible to downsize the power supply. In addition, the lifetime of LEDs is 5 to 10 times longer than that of high-pressure mercury short arc lamps, therefore also reducing the replacement frequency.
There are many benefits to replacing them with LEDs besides being mercury-free.
Summary
Several years ago, when the current RoHS exemption was being considered, it was recognized that there was no alternative technology to replace high-pressure mercury short arc lamps for UV light sources in photolithography applications. Through the rapid technological progress of UV LEDs, it became clear that LEDs can be not only an alternative technology, but also offer significant benefits such as reduced power consumption and CO2 emissions. This post also demonstrates an actual example where UV LEDs were adopted at a manufacturing site.
Nichia believes that by further improving the performance of UV LEDs and discovering effective ways to use them, the extension of the RoHS exemption currently granted to mercury lamps will no longer be necessary for all photolithography applications.
Nichia continues to make efforts towards the realization of a mercury-free and carbon neutral society through the elimination of all mercury lamps.
TrendForce 2024 Deep UV LED Market Trend and Product Analysis
Release: 31 March, 30 September 2024
Language: Traditional Chinese / English
Format: PDF / EXCEL
Page: 50-60 / Semi-Annual
If you would like to know more details , please contact: