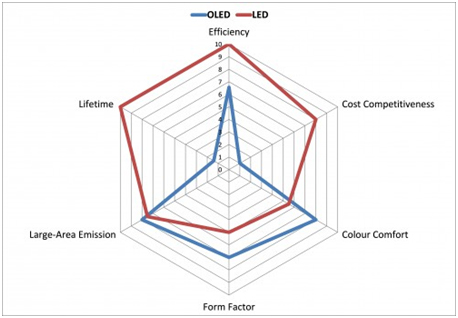
Earlier in May, Panasonic Corp announced that it has developed a white OLED with the world's highest luminous efficiency of 114 lm/W. Improvements in the efficiency of this OLED device were due to the company's focus on optimizing light extraction technology for an all-phosphorescent white OLED. As a reminder, Panasonic Idemitsu OLED Lighting, a joint venture of Panasonic and Idemitsu, began volume production of OLED lighting panels in October 2012. The partnership was established back in 2011,with an initial investment of $182 Million, Panasonic having a 51% stake and Idemitsu 49%.
Konica Minolta is going ahead with commercialization as well, making its Symfos OLED lighting panels available in a 5-panel sample set (7.4cm x 7.4cm with a thickness of just 1.9mm). Using Konica Minolta's proprietary blue phosphorescent materials, the panels deliver luminous efficiency of 45lm/W and have a lifetime of 8,000hrs.
This luminous efficiency, according to roadmaps by Konica Minolta, is expected to reach 120lm/W by 2015, which is close to the efficiency LED lighting (around 140 lm/W). These efforts of improving efficiency, something that's also witnessed in other parts of the world like the USA or Europe, are in contrast to what is observed in Taiwan for example, where the focus is on expanding capacity for existing OLED panels, without significant work on performance optimization.
Identifying the right solutions for encapsulation of flexible OLEDs has been a top priority for most companies developing OLED technologies. Flexibility in form factor without compromising lifetime is seen as one of the key selling points of OLED lighting hence, developments of flexible barriers for oxygen and moisture are paramount for the future of OLED lighting.
One of the approaches is that of Asahi Glass Company, that first demonstrated its flexible glass at SID's Display Week in 2011. At only 0.1mm thick, the company's engineers came up with an easier way to handle the ultrathin glass: The technique uses an adsorption layer to temporarily attach the 0.1-mm-thick sheet to a 0.5-mm-thick sheet of carrier glass, which is much easier to handle during fabrication of devices.
Asahi's "sheet-to-sheet method" of handling ultrathin glass allows the glass to be handled in existing manufacturing lines, the company says. The carrier glass can be easily removed, and the ultrathin glass substrate combined with the carrier glass does not directly contact manufacturing equipment, preventing the glass substrate from being scratched. The resulting resistance to heat and chemical treatments used for manufacturing displays is as high as that of a normal glass substrate.
AGC's ultra-thin sheet glass on carrier glass and rolled into a coil.