Fraunhofer Institute for Applied Polymer Research IAP partnered with Freie Universität Berlin and Technische Hochschule Wildau to work on a research project for developing a novel 3D printing process that enables easier and more efficient production of three-dimensional components using UV-LED-curable reactive resins. This allows printing times to be reduced compared to conventional additive manufacturing processes.
According to the researchers, the new project, named BUERMa, standing for "Belt deposited, double UV-cured materials for 3D engineering - overcoming the property limits of today's Rapid Manufacturing,” aims to simplify 3D printing manufacture. The process uses synthetic resins to replace the common material which is difficult to manage during the heating and cooling process. Synthetic resins can be cured by UV irradiation and will hardly change shape once formed; thus, the material serves as better component for 3D printing.
The team explained that in the BUERMa process, a viscous reactive resin is mixed with a photoinitiator, introduced into a metering unit and pressed through a nozzle with a diameter of 0.1 to 0.6 millimeters. The material is then deposited in pre-programmed tracks and directly irradiated with UV LEDs. This process ensures that the resins cross-link with the aid of the photoinitiator and form an extremely stable polymer network - they cure immediately in a controlled manner. The layers are then built up in layers, as in the FDM process, for example.
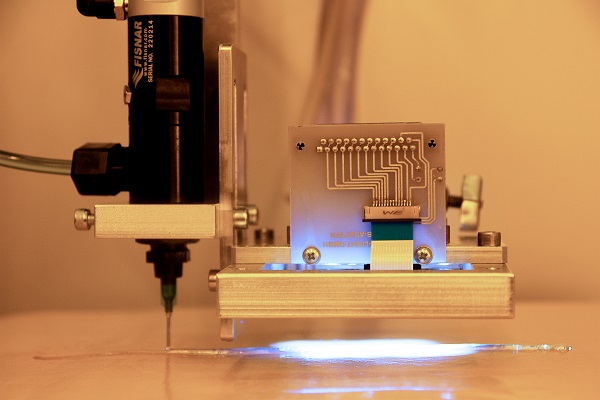
(Image: Fraunhofer IAP)
"Crosslinking is an extremely fast process. The resin cures quasi at the moment the UV light penetrates. This means that the printed component can only warp slightly and can be printed even faster," explained Christian Dreyer, the project leader.
Besides building advanced 3D printer system for industrial applications, the team also hopes to adapt resin formulations for other technical applications with further investigations planned to optimize process windows and parameters. Important factors influencing quality are the printing and conveying speed, the dosing method, the viscosity of the resin, the UV intensity and the irradiation method. Within the scope of the project, a compact print head equipped with UV LEDs will be designed and developed.