Tridonic Dresden, the former LEDON OLED lighting, and Franhofer COMEDD are presenting a desk luminaire with flexible OLED at the Plastic Electronics 2013. The product is the result from a joint OLED project R2flex that was focused on the production of highly efficient organic devices on flexible substrates, manufactured in a roll-to-roll process technology. The project that successfully concluded recently, was funded by the Federal Ministry for Education and Research Germany (BMBF) with a total sum of about 11 million Euros over a period of 2.5 years.
The overall aim of the joint project R2Flex included the development of essential components for highly efficient OLED technology. The OLED should be processed in a roll-to-roll process technology on cost-effective substrates, especially on metal foil. This technological approach should help solve a main problem of the production of OLED: to be able to offer and use OLED for lighting and signage applications, low costs are essential. This key fact could not be achieved by the conventional technology approaches because of the high costs of the coating technologies and materials.
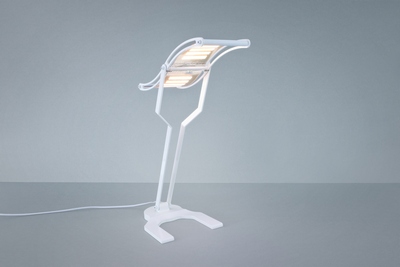 |
R2Flex desk luminaire with flexible OLED on metal substrate. (Photo: Tridonic Dresden) |
OLED roll-to-roll technology for flexible substrates
Fraunhofer COMEDD has improved its roll-to-roll research line, which consists of a vacuum system for the evaporation of organic materials. Furthermore, it includes a coating and lamination system, which can be used under nitrogen atmosphere, and an optical inspection system for defect control and processes monitoring on flexible foils. Within the R2Flex project the OLED technology of established processes could successfully be transferred from rigid substrates to roll-to-roll processes. Especially, the processes for patterning of substrates and encapsulation of the foils were developed. However, one of the most important key challenges of the investigations was the deposition technology of complex OLED structures. To achieve e.g. white OLED, many different layers with a layer thickness in the range of several nanometers have to be deposited precisely on top of each other. Performing this process within a roll-to-roll line was a complex task. Nevertheless, a white OLED could be demonstrated successfully on metal foil.
 |
White OLED on metal foil. (Photo: Tridonic Dresden) |
OLED product integration
Next to the manufacturing of OLED on flexible substrates also aspects of their integration for possible products have been investigated by Tridonic Dresden GmbH & Co. KG. Therefore, Tridonic Dresden evaluated technologies for the secure and cost-efficient electrical contacting of flexible OLED on metal substrates and their integration in luminaires. Resulting from this the problem of contacting through the barrier film could be solved together with Fraunhofer COMEDD. Such a solution has been integrated successfully into the roll-to-roll research line of Fraunhofer COMEDD.
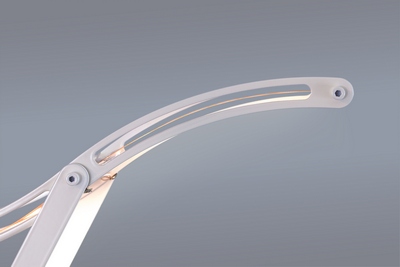 |
View on the curved flexible OLED. (Photo:Tridonic Dresden) |
Project results combined in a desk luminaire
As a result of the joint project R2Flex a demonstrator in form of a gracile desk luminaire could be manufactured. Therefore, two flexible OLED on metal substrate have been used, which were produced at Fraunhofer COMEDD. The modules were serially connected via flexible contacting. The luminaire combines both straight and curved shapes. The curved shape of the head section of the luminaire impressively presents the flexibility of the OLED.