Application of high-end white light illumination:
Laser headlights and laser projectors have been a trend in the use of high-end illumination over the past decade. Initially, white light was created by using blu-ray LD and Ce: YAG fluorescent ceramics (headlights) or by casting LD on a phosphor painted color-wheel plate (projector). As the laser power rises, the heat generated by the conversion of electro-optical efficiency increases the temperature and deteriorates the quantum conversion efficiency of the fluorescent material, which is known as thermal quenching, resulting in light decay. Fig. (1) shows the comparison of the luminous intensity of fluorescent single crystal, fluorescent glass, and fluorescent ceramics that varies with temperature. It is obvious that single crystal has a relatively low thermal quenching performance at high temperatures due to its high thermal conductivity.
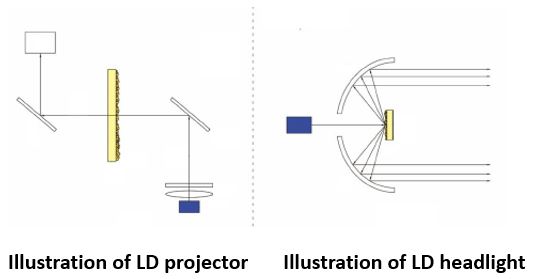
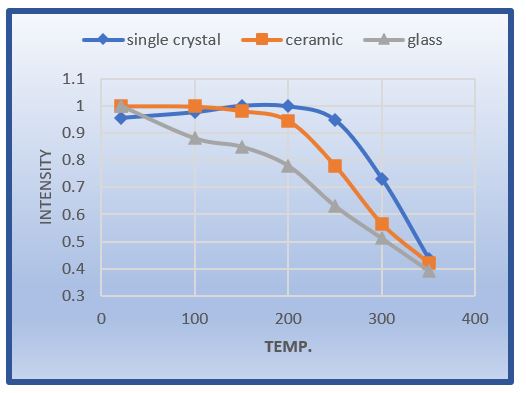
(Fig. 1)
As a result, fluorescent single crystal seems to be the primary option for headlights and high-lumen (> 20,000 lumens) projectors with LD-based light engines. However, the fluorescent single crystal cannot replace the original fluorescent material directly under the existing optical design structure. A re-design of the optical design is necessary, but it increases the cost and design risk for the manufacturer.
New solution — heat-resistant phosphor:
Taiwan Applied Crystal (TAC) has successfully developed the heat-resistant phosphor that is different from the conventional ones (Fig. 2). Under operating temperatures higher than 200°C, its luminous intensity is up to 20% higher than that of conventional phosphors (Fig. 3). This means that heat-resistant phosphors have better QE and luminous intensity under the condition that the original optical design does not increase the design or cost of the heat-sink device. This allows lighting devices with LD-based light engines to successfully replace LED-based light engine lighting or projectors more simply and cost-effectively.
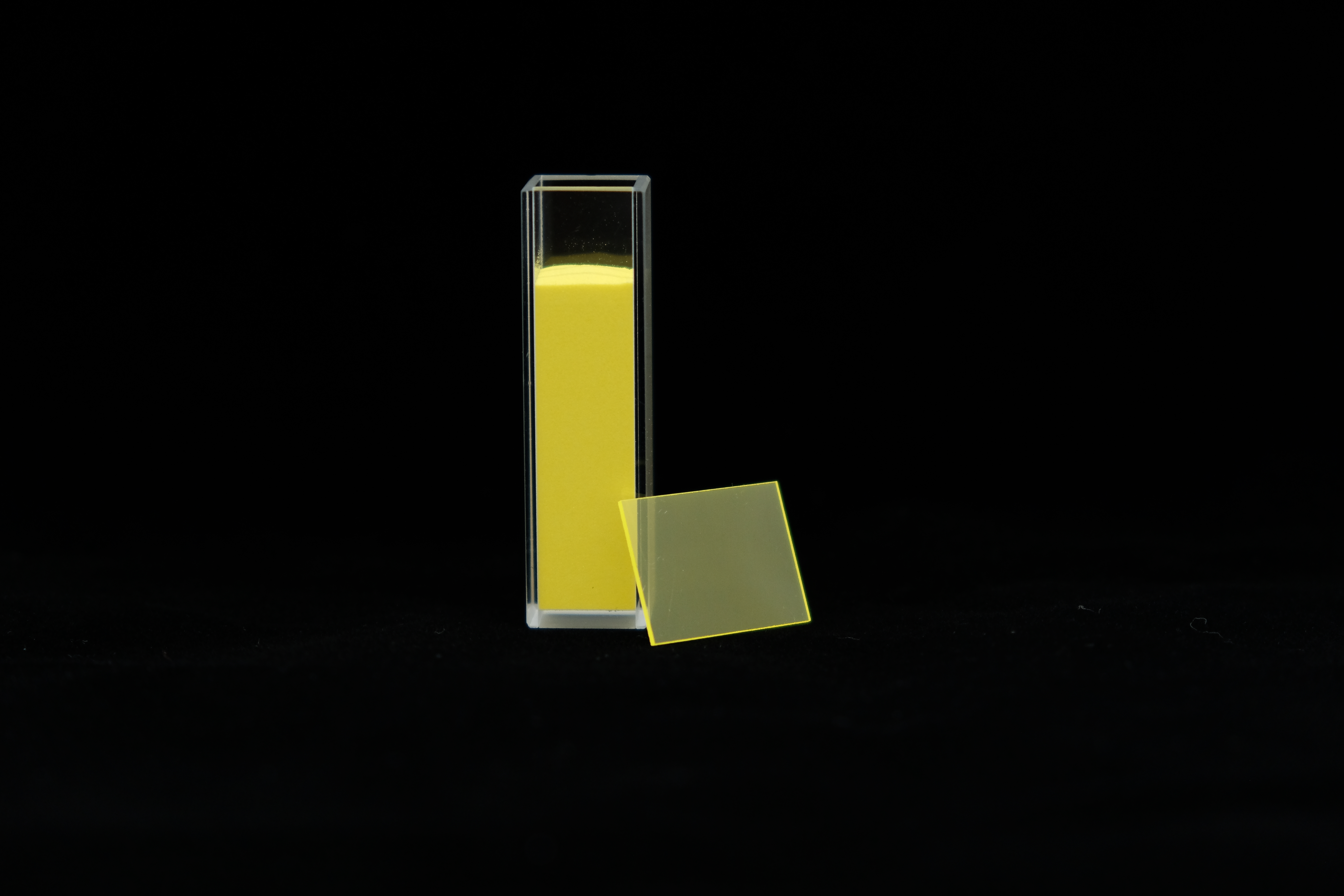
(Fig. 2)
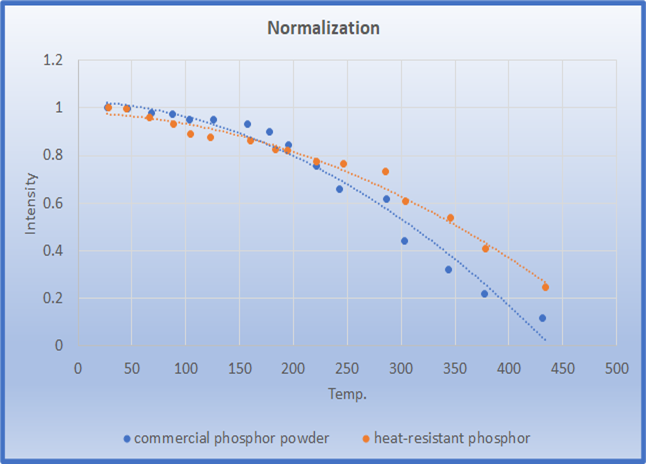
(Fig. 3)