Most speakers highlighted niche market applications including UV LED, IR LED and automotive lighting market applications and opportunities, during the afternoon session of LEDforum 2015 this year, which took place last Friday at National Taiwan University Hospital International Convention Center in Taipei, Taiwan.
UV LEDs hold huge market potential in curing applications for machines, high speed printing, dispensers, lamination machines, PCB, and LCD exposers, said Charles Wei, Chairperson of High Power Lighting (HPL).
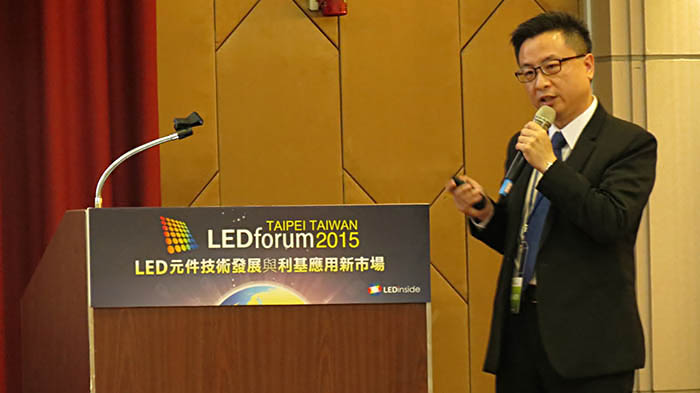 |
Charles Wei, Chairperson of High Power Lighting (HPL) during his presentation at LEDforum 2015. The Taiwanese company specializes in UV LED production and applications. (Photo courtesy of LEDinside) |
Wei shared some of his insights in the UV LED curing application market and technology requirements for the field. His observations as following:
Wavelength requirements: High power LED packages will mix several different UV-A LED wavelengths, which comprises 365 nm, 385 nm, 395 nm, 405 nm and 430 nm. These light module designs have to reach uniform light distribution, one failed LED light source would ruin the entire curing process. This is one of the greatest challenges in designing UV LED light modules for curing applications. If manufacturers want to scale back on customized large light sources, one option is joining small light modules together, which prioritizes seamless splicing technology.
Optic designs: Depending on the product’s uniform lighting distribution and working distance requirements, the beam angle has to be smaller than 60 degrees.
UV LED light irradiance is completely reliant on the working distance (1 mm-150mm), and calculations based on irradiance ranges between 4W-20W/cm2.
Uniformity of UV LED lights must reach at least 85% in curing applications.
Cooling system: Depending on the facility environment demands, the cooling system might use water or air based cooling systems. LED air cooling systems cost less than water cooling systems, but can accumulate dust, and are noisier. The water cooling system could be used in higher wattage applications, but not in cleanrooms.
UV LED applications in exposurers have been fairly difficult because of UV LED optic designs requiring collimated light designs. Light beams emitted from mercury lights can become collimated light after travelling through winding glass tubes, but if LEDs used the same solution light emitted from LEDs would become dimmer and lead to unnecessary lumen output loss.
In exposurers UV LED optic designs demand collimated light, which requires a beam angle between 1°to 6°.
UV LED irradiance in exposurers requires a working distance of 50 mm-150 mm, which is roughly equivalent to 100mW-1W/cm2.
The LED’s uniformity requirements is similar to other UV LED applications 85%.
HP Lighting’s UV LED optic designs utilize a special secondary optic design, which can achieve a collimated beam angle of less than two degrees, and more uniform lighting optic designs. These make the products very suitable for exposure designs.
All these curing market technology designs need to be discussed with clients. Even with a same type of machine, it has to be adjusted to meet clients facility environment and is a market that requires high levels of customization.