Headquartered in Hong Kong, Maven Optronics International (Maven Optronics) has wholly owned subsidiaries respectively in the Silicon Valley in U.S., Hsinchu in Taiwan, and Jiaxing in Zhejiang Province, China. The company successfully developed patented advance thin film coating technology that can be applied in semiconductor manufacturing and even in white
LED phosphor coatings that can be made to develop phosphor film products and CSP LEDs. The company is currently rapidly expanding in the European and Asian market. Based on LEDinside observations of flip chip LED and CSP LED market developments, Maven Optronics phosphor film product range is very unique. In an exclusive interview with LEDinside, the company founder and President Dr. Chieh Chen spoke to LEDinside about the company’s phosphor coating technology and related CSP LED applications.
In phosphor film technology, conventional phosphor coating process involves dispersion or spray-coating to mix the phosphor powder and adhesive together, said Chen. If the phosphor dosage density is insufficient, the distribution of the powder over the LED surface will be lumped and non-uniform, making it difficult for the phosphor film to achieve conformal and uniform light output. Resulting phosphor coating uniformity and reliability from conventional phosphor film coating technology is usually less ideal.
Maven Optronics phosphor coating technology separates adherence and coating, and uses two different equipment in a vacuum chamber to coat phosphor powder onto flip chip LEDs. The company’s phosphor coating technology employs a process similar to semiconductor manufacturing to improve phosphor film uniformity, consistency and reliability. Depending on the clients optical application demands, the phosphor powder and adhesives can be made into a layer-by-layer phosphor structure.
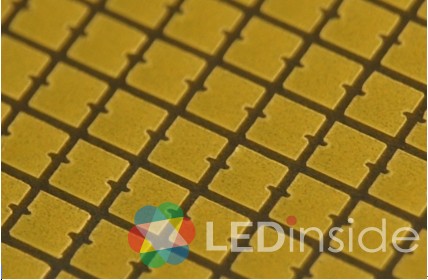 |
Notch-patterned Phosphor Layer (Dual Notches) for Vertical Chips |
In advanced CSP manufacturing process, the company’s patented phosphor layer-by-layer technology is extremely precise. Following the attachment of the silicone resin, the LED color performance falls in the high bin rate, and color uniformity. Additionally, phosphor powder usage volume can be halved with this method.
In contrast to the average phosphor powder spraying technology, the company’s distinct adherence and coating methods enables layer by layer conformal coating, since the phosphor coating powder process onto the surface proceeds silicone resin coating. Hence, the product is able to achieve color uniformity performance previously unattainable by same types of products, and the CSP LED beam angle is expanded to 120 degrees to 170 degrees.
 |
Wafer Level Phosphor Coating Service |
CSP LED products greatest advantages is in the flash LED and backlight markets, and the chips consistency and reliability can be improved through phosphor coating. It is projected CSP LEDs will be applied in automotive and lighting in the future. By incorporating red emitting KSF and green emittingβ-SiAlON phosphors in layer-by-layer phosphor film used in the CSP LED, the NTSC color gamut performance can be raised to above 90% to match OLEDs. Currently, CSP LEDs unique design and beam angle can reach 170 degrees. If the technology is applied in tube light markets, it could improve product costs and retail prices.
 |
5-side-light-emitting CSP |
(Author: Joanne Wu of LEDinside, Translator: Judy Lin, Chief Editor, LEDinside)