Being an important component in display technology, LEDs have been continuing the improvement in power-saving and display capabilities. Mini LED backlights, Mini LED RGB and Micro LED also appear on the stage to meet various requirements of products targeting different applications.
Mini LED backlights, which have been officially introduced into the market in 2H18, will be facing off OLEDs soon and become a new opportunity in the panel industry, according to LEDinside’s 2019 Mini LED and HDR High-Class Display Market Report.
EPISTAR, a global leading brand and provider of LED dies and epitaxial wafers, has not only been pushing the development of various LED technologies forward, but is also a key promoter of Mini LED backlight technology.
EPISTAR has already shipped small amounts of Mini LED backlight products since last year, which were used in gaming notebook and high-end displays. Displays using Mini LED backlights are featured with local dimming function, demonstrating high contrast with high-dynamic range.
In order to understand the strengths of LED backlights, LEDinside interviewed two senior directors at EPISTAR, Dr. S.Y. Deng in Product Management under the Sales and Marketing Center; and Dr. Kirin, Lee in Technology under the LED Chip Research and Development Center. They shared the energy saving performance of LED backlight displays and how EPISTAR uses innovative technology to overcome the bottlenecks during development.
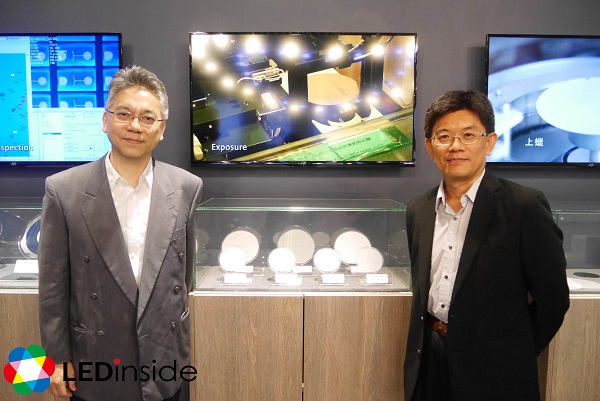
(Left: Dr. Dr. S.Y. Deng; right: Dr. Kirin, Lee)
HDR Dynamic Backlight Technology Ushers in New Testing Method of Energy Star 8.0
“The new backlight technology is like a low resolution black-and-white screen that provides a richer dynamic display experience,” said Dr. Deng. The biggest difference between Mini LED backlight technology and traditional backlight strips lies in that Mini LED backlights may be used for local control, meaning that only the LEDs within bright regions will be lit up while those in dark regions are turned off accordingly.
With local light control, LED backlight technology is not only able to provide stark contrasts on the screen that rival those by OLEDs, but also save more energy since LEDs do not have to be constantly lit up. The newly released Energy Star 8.0 specifications have hence introduced new methods of power consumption measurement, allowing the exceptional energy-saving performance of LED backlights to fully shine.
Dr. Deng explains that past standards assigned to LED tubes and other traditional backlight technologies do little to highlight the regional lighting capabilities of Mini LED backlights. Players in the industry thus hastened the introduction of the Energy Star 8.0, which utilizes many different methods of measurement that no longer measures the fixed performance per watt value. Instead, the new version measures power consumption by playing dynamic content on the screen, which genuinely reflect the energy-saving capabilities of backlights. The more the display are finely divided with different zones and the higher the dynamic contrast, the more energy can be saved. The new version properly reveals the energy saving performance of Mini LED backlit TVs and displays.
“A 4K, 65-inch LED backlit LCD TV which meet the criteria of Energy Star 8.0 consumes only around 100 watts per hour!” Dr. Deng further explained that OLED TVs of the same size consume up to 500 watts per hour, which equivalent to that consumed per hour by a microwave.
EPISTAR’s Proprietary Reflector Provides Customizable Beam Angles for Mini LEDs
Although the superb energy saving performance gives Mini LED backlit LCD TVs an edge, there are still difficulties in manufacturing. EPISTAR thus shared its viewpoint as a LED supplier.
In connection with the challenges in chip die manufacturing introduced by Mini LED backlight, Dr. Lee commented that “the key of chip die design lies in increasing sources and reducing cost.”
By increasing sources Lee referred to boosting the luminous efficiency (WPE rate) of LED dies. EPISTAR has always been a bright shining star in the industry, and the dies it produces boasts advantages both in the power output of light and operating voltage. Its WPE rate even far surpasses that of other players.
Furthermore, by shrinking chip down to Mini LED scale, the backlight zone can be divided into many finer regions to be controlled separately, which is also an important feature to meet the standard of Energy Star 8.0. Meanwhile, the thin outline trend in premium TV designs also require thinner backlight module, which might create light spots due to the lack of light-mixing distance. One way to solve the problem is to use more LEDs and spread out the light. However, EPISTAR’s light-saving solution is to change the beam angle of Mini LED and reduce the number of chip usage, which also leads to production cost reduction.
With its proprietary reflector, EPISTAR has developed Mini LEDs with customizable beam angles. Beam angle of LEDs is usually around 140 degrees, but EPISTAR’s technology can extend the beam angles up to 150, 160 or even 170 degrees.
According to Dr. Lee, larger beam angles may reduce the number of LEDs required, and customized reflector technology also helps to spread the LED beams around, smoothing out the distribution of backlight modules and minimizing the effects of light spots. In this way, light guide plates and related spreading films may be simplified, allowing compacted display with reasonable cost for high end products.
At the same time, since the local dimming dynamic display technology in Mini LED backlights have to be linked and synchronized with the front-end display image, the chips of a few individual areas may have to spike up in brightness beginning from a completely dark state. Therefore, the design of the dies themselves and the technology needed to integrate drivers and the system all pose new challenges.
Mini LED Backlight Technology Ready to Roll with Automotive Applications Becoming the Spotlight
How to balance energy conserving advantage of Mini LED backlight technology and the high costs associated with new structures has become the issue that both EPISTAR and customers must solve.
Dr. Deng’s indicated that costs for Mini LED backlight display production include costs for chips, transferring and backplanes. When dimming zones increases, the number of LED used will go up. If there are 1000 dimming zones, the number of LEDs used may range from thousands to ten-thousands according to different design. As a result, the cost for transfer and bonding will rise. EPISTAR’s current goal is to drive high-end products on shelves first, hoping to reduce the cost price through quantity and push further development.
It was expected that mass production for Mini LED backlight products will take place this year. But the on-going trade dispute between the U.S. and China has impacted the market, leading to delays of new products launch. Nevertheless, EPISTAR has confidence in its own product and technology. Many products have passed tests with mature technology. EPISTAR expects that Mini LEDs applications will expand by the end of 2019.
Speaking of future applications for Mini LED backlight technology, EPISTAR is optimistic about the potential of automotive displays. The developing of self-driving cars set the drivers free from driving and thus spurs the development of in-car entertainment and communication. The power-conserving feature of LED also satisfies the need of electric cars for energy-saving.
Dr. Deng noted that technology will continue to evolve as human habits change. LED provides opportunities for innovative applications in the future. EPISTAR, as a leading company in the LED industry, will also continue to promote novel technologies to realize the infinite possibilities of LEDs.