According to LEDinside, the global market size of micro LED is expected to grow to US $1.12 billion in 2020 and US $3.18 billion in 2025. In the end, a variety of products (BLU and RGB displays) with micro / mini LEDs as individual pixels are expected to be introduced to the market. However, technologies that can deliver large quantities of LED chips to the substrate at a time are still under development, and technologies for repairing defective mini LED chips are needed.
Before the emergence of the early micro LED products, companies in Korea, Taiwan and China have focused on developing mini LED products in 2018. In case of BLU application, Chinese and Taiwanese companies will launch blue LED Chip for BLU (Back Light Unit) of smart phone and monitor to provide HD local dimming function at the beginning of 2019. Other applications of mid- and large- sized display products using RGB chips are expected to lead Korean companies in the market. However, they must reduce the manufacturing cost of display products and increase reliability.
Compared to the development stage of micro LED manufacturing process, mini LED products can apply existing equipment and process. However, in order to economically produce products through cost reduction in all aspects of materials, processes, and equipment, it is very important to select the bonding material between the mini LED chip and the PCB and the final molding material (underfill) of module containing blue LED or RGB chips.
Currently, manufacturers in Korea, Taiwan and China are using 1) conventional solder paste bonding material with solder powder and flux, and 2) new epoxy-based epoxy solder paste (ESP) as a binder. The final molding material to protect BLU and RGB LED bonded chips is used with epoxy or silicone type materials.
This article explains the result of applying ESP and molding materials to mini LED products. Compared to conventional solder paste using rosin flux, epoxy-based ESP bonding material have the following advantages,
- since there is no residue flux, no cleaning process after reflow is necessary.
- cured epoxy can block the flow of melted solder throughout the subsequent heating after reflow process.
- the cured epoxy increases the bonding strength between the mini LED chip and the PCB.
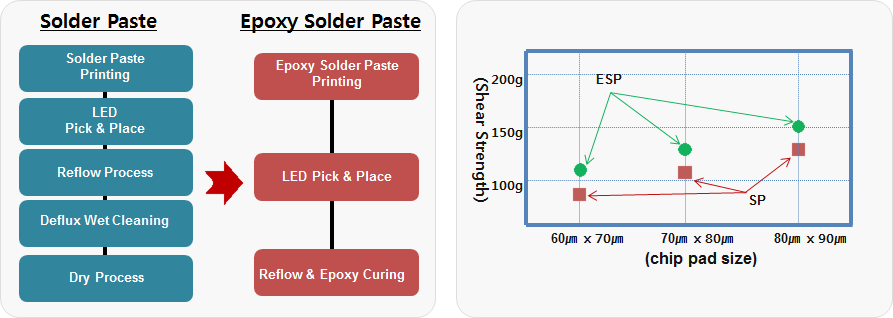
Left: Figure 1. Comparison of conventional Solder Paste and ESP materials
Right:Figure 2. Result of Shear: Strength with conventional Solder Paste and ESP materials
As shown in Figure 1, eliminating the cleaning process not only saves the cost, but it also has the benefit of protecting environment by removing the wet process from the production line. Figure 2 shows the customer’s ESP shear strength test results, which is more than 30% higher than the ESP shear strength of conventional solder paste, making ESP suitable for low adhesive strength reinforcement and mini LED detachment during cleaning process. Small pad size mini LEDs can cause separation in the entire PCB surface due to low bonding strength.
The role of molding material in mini LED products is to increase the bonding strength and protect chip, and different characteristics are required depending on the BLU and RGB displays. For BLU products, BLU products typically use a flexible PCB, so a low curing temperature is required to prevent PCB warpage during bonding process. On the other hand, in RGB display, the dozens ㎛ gaps of the sub-pixel needs to be filled with epoxy of the black material(BM). The role of BM in epoxy blocks light interference between RGB colors.
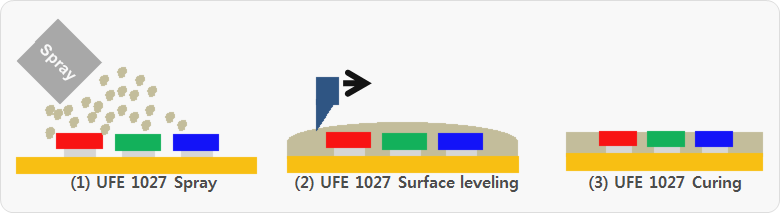
Figure 3. Spray coating process of UFE1027 molding material
Currently, Hojeonable Inc. offers ESP and molding materials to its customers, and the latest practical application is shown in Figure 4. Hojeonable Inc. is a specialist in mini/micro LED materials and we are honored to hear from you about your product development needs.
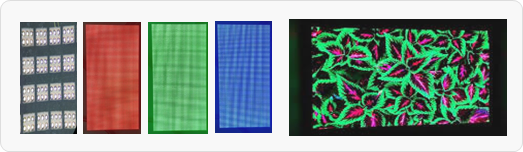
Figure 4. RGB PCB & its Application Display
For further details, please refer to the contact information as below:
Ms. YJ Lee
Tel. +82-42-824-9538
Mob. +82-10-5029-5681
Email: yjlee@hojeonable.com
Website: www.hojeonable.com
(The article was written by Donghae Lee, Oversea sales team, Hojeonable Inc.)