Consumers globally are using touchscreen displays every day in a growing array of electronics, from TV to smartphones to mobile gaming consoles to in-car navigation systems.
With heightened demand for touchscreens, electronic manufactures are increasingly turning to Phoseon Technology’s UV-LED curing for its many benefits in adhesives bonding applications.
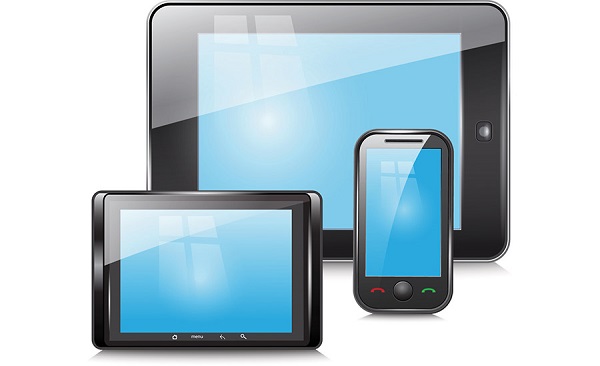 |
Electronic manufactures are utilizing Phoseon Technology’s UV-LED curing to bond adhesives when manufacturing touchscreen displays for electronics such as smartphones, tablets and in-car navigation systems. (Image: Phoseon Technology) |
Phoseon’s unique UV-LED curing provides a consistent and reliable process to assemble touchscreen displays, whether it be to bond a cover glass to a liquid crystal display (LCD) or an organic light emitting diode (OLED) screen, or curing adhesives on a smartphone’s ultra-thin border to prevent light leaking out through the edges. Phoseon’s solution also cures the encapsulation layer of the OLED display, which is an essential element to prevent the damage of organic elements from oxygen and moisture over its life time.
“Phoseon’s UV-LED technology is used to cure the UV adhesive, typically an acrylic formula, creating a strong and uniform bond between each touchscreen display layer,” said Rui Zhou, technical marketing engineer at Phoseon Technology. “The benefits of UV-LED curing include excellent optical properties such as better light transmission, vivid color display and reduced glare.”
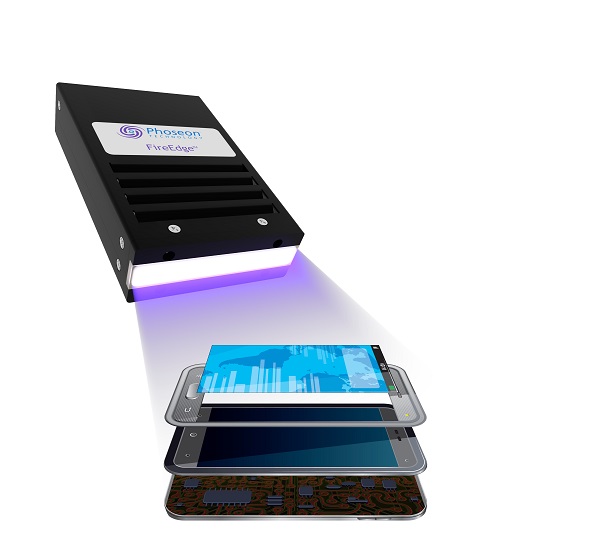 |
Phoseon Technology’s FireEdge™ is an air-cooled UV LED curing lamp for curing adhesives used in manufacturing touchscreen displays for electronics. (Image: Phoseon Technology) |
Faster Monetization of Manufacturing Investment
Phoseon’s technology, which has been used commercially for more than 12 years, is a photopolymerization process that uses UV-LED light to rapidly change or “set” a liquid to a solid, usually within seconds, without the use of heat or solvents.
Zhou notes that UV-LED curing also offers electronics manufacturers high yield rates and productivity due to a safe, consistent and stable process without damaging heat-sensitive components. “In addition to its quick-drying capabilities, UV-LED curing creates very little heat that can damage sensitive components used in electronics — a critical element that cannot be replicated with other curing methods,” said Zhou.
“UV-LED curing has no moving parts, virtually eliminating down-time for maintenance and repairs,” said Zhou. “In addition, UV-LEDs last longer and require less energy to operate than traditional arc lamps or metal halide lamps, reducing operation costs and energy usage by up to 70 percent.”
Furthermore, because UV-LED curing does not contain mercury, which is used in arc lamps, it produces no ozone emissions or hazardous waste concerns, and are environmentally friendly and safe.
In addition to display bonding, Phoseon Technology’s UV-LED technology also is used in a wide range of other applications, such as narrow-web, wide-web and decorative printing, manufacturing wood, and curing wood and filament coatings.