LEDs are up to 80 percent more energy-efficient than normal light bulbs and last around five times as long as energy-saving light bulbs. As a result they are being used more and more frequently as a source of light. Nevertheless, white LEDs still have room for improvement, as current manufacturing processes are either very expensive or result in the lifetime of the LEDs being reduced. Researchers at FAU have now developed a new, rather unusual manufacturing method: their LEDs are partly made of fluorescent proteins.
In our homes and in street lights, in traffic lights and in screens – LEDs are an essential part of our everyday lives. They have a long lifetime, are highly energy-efficient and environmentally friendly, and require little maintenance – to name just a few of their beneficial qualities. However, manufacturing white LEDs is complicated.
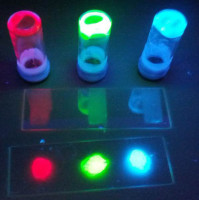 |
The image shows the gel-like networks that consist of a concentrated aqueous protein solution and a polymer compound. (Photo Courtesy of Michael Weber) |
Finding the perfect combination
Research is currently focusing on two ways that could be used to make white LEDs in the future, both of which have their disadvantages. In the first method, thin layers of inorganic materials such as phosphorous or rare earth elements are applied to a blue LED. The resulting LEDs have a long lifetime and emit light with the optimum strength. However, as rare earth elements are used and the manufacturing process is complex, the production costs are extremely high and are not sustainable. The alternative is to use organic LEDs in which several organic semiconductor layers are sandwiched between two electrodes. These LEDs have a lower performance and shorter lifetime than their inorganic counterparts. The optimum solution, therefore, would be a combination of the two versions which has the advantages of both methods.
FAU researchers have now succeeded in creating exactly this kind of combination – with the help of fluorescent proteins that are embedded in a rubber-like material and applied to an LED. Dr. Rubén D. Costa from FAU’s Cluster of Excellence ‘Engineering of Advanced Materials’ (EAM) and his colleague Prof. Dr. Uwe Sonnewald from the FAU Emerging Fields Project ‘Synthetic Biology’ collaborated on the research.
Proteins in a gel bed
‘The fluorescent proteins combine the desired elements,’ explains Dr. Rubén D. Costa from the Division of Physical Chemistry I, ‘They are environmentally friendly and inexpensive to manufacture. In addition, the proteins allow the colour setting – either coloured or white – to be controlled easily.’ However, there is one snag: the proteins are only stable in an aqueous buffer solution, meaning that it is not possible to use standard coating procedures. The researchers also had to ensure that the proteins would work stably under various environmental conditions, such as at high temperatures or humidity.
Their solution was to develop a new coating technique. The embedded the proteins in a gel that consisted of a concentrated aqueous protein solution and a polymer compound. The polymers bind the aqueous protein solution to make a gel-like network while ensuring that the necessary moisture is retained. The gel is then vacuum dried, turning it into a rubber-like material that is suitable for multilayer coating of LEDs and protects the proteins from external influences.
‘With our method we have managed to create long-lasting and efficient white LEDs using an environmentally friendly and inexpensive manufacturing process. This is a pioneering method for future generations of LEDs,’ Dr. Costa explains delightedly.
Excellent research
Around 200 researchers are developing new materials at FAU’s Cluster of Excellence ‘Engineering of Advanced Materials’ (EAM). In over 90 projects, researchers from nine disciplines (applied mathematics, chemical and biological engineering, chemistry, electrical engineering, computer science, medicine, mechanical engineering, physics, and materials science) are working on each stage of the process chain, from basic molecules to finished materials.
FAU established the Emerging Fields Initiative (EFI) in 2010 with the aim of identifying outstanding and preferably interdisciplinary research projects at an early stage, and providing them with support and funding in a non-bureaucratic way. After the first two rounds of applications, 18 EFI projects have so far received a total of 12 million euros in funding.
The researchers recently published their findings in the renowned journal Advanced Materials. The article is available at http://dx.doi.org/10.1002/adma.201502349.