The aim is to increase the performance and lower the costs of laser systems for material processing
As part of the ‘Integrated Microphotonics’ initiative, Osram Opto Semiconductors is coordinating the IMOTHEB project (Integrated microoptical and microthermal elements for diode lasers of high brilliance). The aim is to improve the performance of laser systems and at the same time reduce production costs. The project partners are DILAS Diode Laser and the Max Born Institute. The project (FKZ 13N12312) runs from October 1, 2012 to September 30, 2015 and is being supported by the German Ministry for Education and Research (BMBF).
Diode-pumped high-power laser systems for material processing such as cutting and welding are playing an increasingly important role in industry. Their advantages over carbon dioxide lasers and lasers pumped with flash lamps are lower operating costs, greater efficiency and smaller size. Fiber lasers and fiber-coupled diode lasers are becoming more and more important for optical material processing. As they become widespread, however, the focus is shifting to the question of costs. Developments that increase the performance of laser systems and at the same time reduce production costs are therefore needed. Infrared semiconductor laser diodes which can be used to pump fiber lasers are key components here. They offer enormous potential for automating production and miniaturizing the systems. Increasing performance, for example, can lead to a reduction in the number of semiconductor chips needed.
The objective of the IMOTHEB project is therefore to investigate new approaches and technologies that may ultimately lead to significant reductions in the costs for the pump modules which include not only the semiconductor lasers but also cooling elements, optics and sensors. There are also plans over the course of the project to September 2015 to increase the output of semiconductor lasers by 40 percent while retaining the same high beam quality. IMOTHEB maps the entire value added chain from the semiconductor chip to the complete laser system. The project partners bring their own specific areas of expertise:
• Osram Opto Semiconductors is coordinating the project and offering its know-how in semiconductors, laser diodes and laser bars; simulations are being subcontracted to the Fraunhofer Institute for Applied Optics and Precision Engineering.
• DILAS is responsible for the assembly technology with improved thermal resistance and higher integration in laser modules, and also for automation in module production.
• The Max Born Institute is acting as a scientific partner, analyzing and characterizing the chips and modules.
Osram Opto Semiconductors has set itself the goal of achieving a higher degree of integration on the semiconductor level, thereby increasing the brilliance of infrared laser diodes significantly. Microoptical and microthermal elements are therefore being integrated directly on the chip. Over the course of the project it is hoped that this will increase output by 40 percent compared with current best values while retaining the same high emission quality. If these high outputs are achieved they will make laser chips ideal for fiber laser pump modules and for fiber-coupled diode lasers. Dr. Alexander Bachmann, project leader at Osram, said: “We need results that bring not only technical but also economic benefits to strengthen our competitive position. Based on results from the project, our brilliant laser diodes should provide more output into the fibers so that fewer chips are needed in the system and the laser systems therefore become more efficient and more cost-effective.”
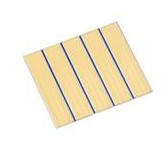
Picture: Osram
Prototype of a high-power laser bar, as developed by Osram Opto Semiconductors in the IMOTHEB project.
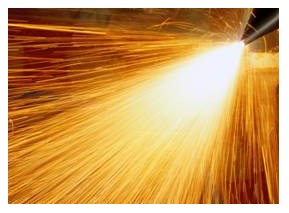
Picture: Osram
Higher output from laser diodes and new automated assembly processes for laser systems target at industrial applications such as laser welding and laser cutting, making them more efficient and more cost-effective.