Dutch R&D institute Holst Centre (set up by imec and TNO) and American ultra-thin ceramics supplier ENrG Inc. have created the first ever ceramic-based, large-area flexible OLED. The device, manufactured on the 20-40 µm thick Thin E-Strate® ceramic substrate, promises a lifetime in excess of 10 years without the formation of blackspots. The ceramic carrier is also easy to handle and capable of withstanding the high temperatures used in display backplane manufacturing and standard sintering processes.
The ceramic substrate used for the 12 cm by 2.5 cm prototype OLED device combines many of the best properties of other flexible OLED carriers. It offers an intrinsic barrier to protect the sensitive OLED from the environment, as with metal foils or flexible glass. But it is much easier to handle than either. Like plastic films, the ceramic offers the potential for semi-transparent devices. In fact, its slight opaqueness actively improves light outcoupling, opening the door to higher devices efficiencies. Unlike plastic films, though, the ceramic can withstand temperatures up to 1000 oC.
"Our Thin E-Strate® ultra-thin ceramic has many plus points over other flexible OLED substrates. It is the only flexible substrate that has both intrinsic moisture barrier properties and high-temperature capabilities, in combination with being both robust and smooth enough to fabricate an OLED device on. The prototype device made by Holst Centre shows the benefits Thin E-Strate® brings new flexible electronics applications," said Kathy Olenick, Technical Marketing Manager at ENrG Inc.
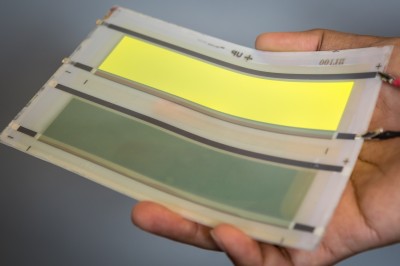 |
Dutch R&D institute Holst Centre (set up by imec and TNO) and ENrG have created the first ever ceramic-based, large-area flexible OLED. (Photo courtesy of Holst Center) |
The materials used to make OLEDs are extremely sensitive to the environment, in particular moisture, and must be protected on both sides. With its intrinsic barrier properties, Thin E-Strate® means OLEDs can be fully protected with just the addition of a top barrier – simplifying production compared to plastic-based OLEDs.
The protection the OLED receives, and hence its potential durability, is typically quantified through its water vapor transmission rate (WVTR). In tests, the Thin E-Strate®-based OLED demonstrated a WVTR below 8.5 x 10-7 g/m2/day. In addition, while most flexible OLEDs require a multi-layer barrier on both sides, the Holst Centre-ENrG device achieved these values thanks to just the ceramic Thin E-Strate®- at the bottom and a Holst Centre thin film top encapsulation, directly deposited by plasma enhanced chemical vapour deposition (PECVD) and printing of a few layers, on top of the device.
"A WVTR of less than 10-6 g/m2/day is widely accepted as a minimum requirement for commercial devices. At this level, it takes over 10 years for deterioration due to moisture to lead to visible black spots. But such a rating is difficult to achieve, and many other flexible OLEDs with single-layer barriers have around 10-5g/m2/day or higher (equivalent to a 1 year lifetime or less). Beating the 10-6 g/m2/day target with such a simple structure shows the excellent protection of Thin E-Strate® and Holst Centre's direct thin film encapsulation stack on top. This approach could help further reduce complexity for flexible OLED production," said Hylke Akkerman, Senior Scientist at Holst Centre.