Laytec has upgraded in-situ GaN LED monitoring system.
LED manufacturers would know the emission wavelength of the final device during MOCVD growth.
Today, according to the Solid State Lighting road map, the wavelength variation across a wafer should be less than 1 nm. This means a less than 1 K (10C) variation of the GaN surface temperature during InGaN MQW growth.
LayTec’s Pyro 400 is widely used for enabling fab-wide GaN surface temperature uniformity in many LED manufacturers production lines.
Meanwhile, more complex LED structures and tighter cost reduction targets need even more advanced in-situ metrology. Figure 1, below, shows such an example; ternary InGaN and AlGaN layers cause emissivity changes that lead to 0.7 K error of the UV pyrometry reading.
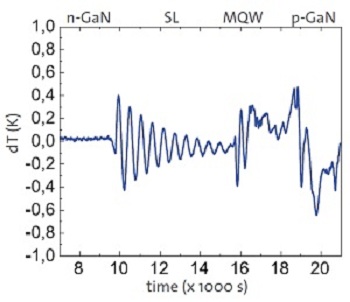
Figure 1: Effect of changing emissivity to UV pyrometer temperature reading: up to 0.7 K errors show up without emissivity correction during growth of a GaN/AlGaN-GaN-SL/InGaNMQW/ GaN structure
LayTec‘s answer to this challenge is the Pyro 400 Gen 2. Along with in-situ UV pyrometry the new generation tool includes real-time UV emissivity correction for enhanced accuracy of GaN surface temperature during growth of more complex LED structures.
A further challenge to reliable GaN temperature control in HB-LED production is the view-port coating.
Figure 2 shows its effect just before maintenance; the UV transmission of the view-port is significantly reduced and an uncorrected UV pyrometer would give a -10 K temperature artefact. Pyro 400 Gen 2 solves this problem,too. Laytec claims the tool automatically senses and corrects these coatings and enables a long-lasting 24/7 accuracy in HB-LED emission wavelength.
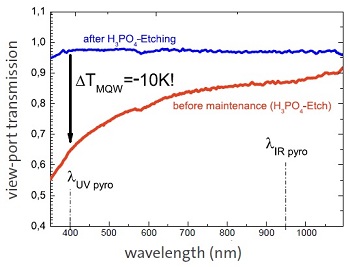
Figure 2: GaN MOCVD view-port before (red) and after maintenance (blue): the transmission at the 400nm detection wavelength of a UV pyrometer is suffering from the window coating (red). The resulting -10K artifact is avoided by Pyro 400 Gen2
Last, but not least, an assisting infrared pyrometer has been integrated into Pyro 400 Gen 2 for simultaneous monitoring of wafer pocket temperature throughout the full LED growth run.