Germany’s OSRAM, the lighting firm under Siemens, is a well-organized company – its OSRAM Opto Semiconductors is speclizaed in LED epitaxy, LED package and is an vertically integrated company. It also has a subsidiary company for LED phosphor business. OSRAM establishes strategic alliances with international major companies and OEMs to strengthen its leading position in the global market.
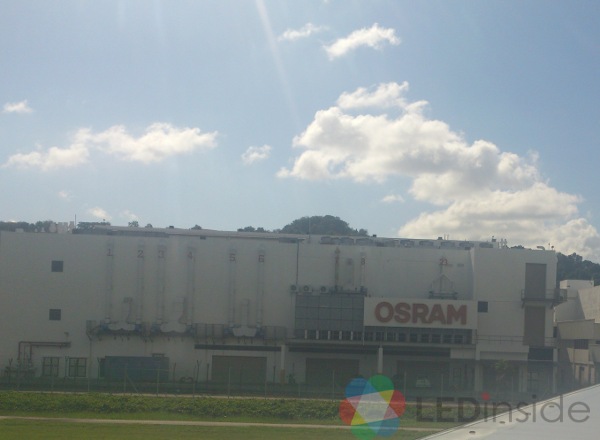
LEDinside staff flied to Penang, Malaysia to do a report on OSRAM Opto Semiconductors’ LED production base (the biggest in the world). The production base manufactures LED chip and LED package and supplies the specialized, consumer, and outdoor lighting markets. OSRAM-OS Penang base is located in the Bayan Lepas Free Industrial Zone Phase One and consists of main plants such as PEN1, PEN2, PEN5, PEN6, PEN8, PEN30, PEN31, and PEN 32. It is almost an OSRAM Park.
The Penang base has 4,600 staff members, covering the initial and latter stages of LED production. OSRAM’s Wuxi base will have 1,600 staff members, which will cover the latter stage of LED production. According to LEDinside observation, Wuxi base will adopt brand new equipment, and therefore, it will require fewer workers.
Forty Years in LED Industry
2012 marks the fortieth anniversary of OSRAM-OS’ establishment. OSRAM entered LED industry as early as 1972 – the company’s predecessor Litronix manufactured LED and was located in Penang. In 1981, Siemens acquired Litronix. In 1992, the company became the Siemens Semiconductors(Today Infineon). In 1999, it became OSRAM-OS.
OSRAM established two epitaxy plants in Rogensburg, Germany and Penang, Malaysia, respectively. The new plant PEN 32 in Penang base started its construction in 2011. It is estimated that after the chip plant in Penang base is established. The two plants will replace the current 4-inch wafer with 6-inch one. With all these improvements, OSRAM’s production of white-light LEDs will grow by 2 times by the end of 2012, supplying the world’s increasing demand. Also, the company’s package revenue is expected to go up along with its LED lighting revenue.

40th Anniversary of OSRAM Penang Base
In terms of the profit brought in by its assorted products, from the highest to the lowest, it goes automotive lighting, consumer lighting, industrial and commercial lighting, LED backlight, optical communication component, and mini projector.
The parent company OSRAM AG’s 2011 revenue amounted to 5 billion Euros, 20% of it was from Asia Pacific region. As for the Chinese consumer market, LED lighting is estimated to account for 20% of the company’s revenue in 2012.
By 2020, value of Chinese LED lighting market will account for 42% of the Asian market and 20% of the global market, generating a revenue of more than 11 billion Euros.
LED FE Site in Regensburg
OSRAM-OS is headquartered in Regensburg, Germany and the company’s main LED expitaxy plant is also located in there. OSRAM-OS sees its Regensburg epitaxy plant as the base for initial production of LED chips and the pivot for the epitaxy R&D of OSRAM. The company’s UX:3 technology was developed in there. LEDinside noted OSRAM’s R&D budget is approximately 300 million Euros, which is commendable.
According to LEDinside’s interview with OSRAM OS, Regensburg’s LED production lines are now undergoing the upgrade from 4-inch wafer to 6-inch one; originally the plant only manufactured 4-inch wafers, but now the plant starts the trail production of 6-inch wafer in small capacity. The capacity will be considerable once the company completes the upgrade from 4-inch to 6-inch.
Regensburg plant’s production covers a wide spectrum of applications such as LEDs, IR LEDs, and LEDs for optical communication components. Products with high added value are manufactured in Regensburg.
LED FE Site in Penang
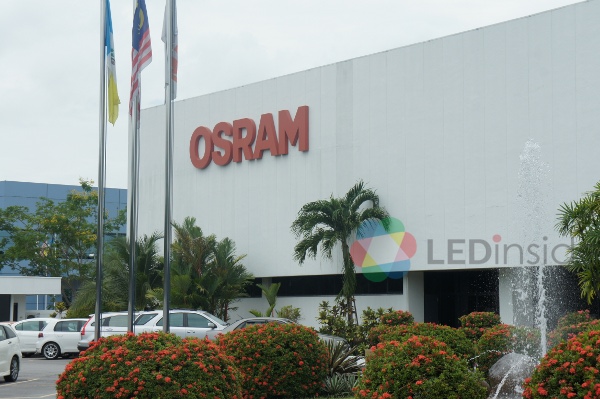
Prior to 2008, Regensburg plant will send LED wafers that have gone through the initial production stage to Penang plant for the latter stage of manufacturing process. However, starting from 2008, OSRAM began building PEN 31 plant in Penang, which will engage in the initial production of LED wafers. After the company finished the construction of PEN 31 in 2009, Penang base became a vertically integrated production base, providing the global and Asian markets with LED chips and packages.
LEDinside took a tour in PEN 31 plant and saw that OSRAM has done an excellent job in quality assurance, management, and R&D and is extremely careful with the safety.
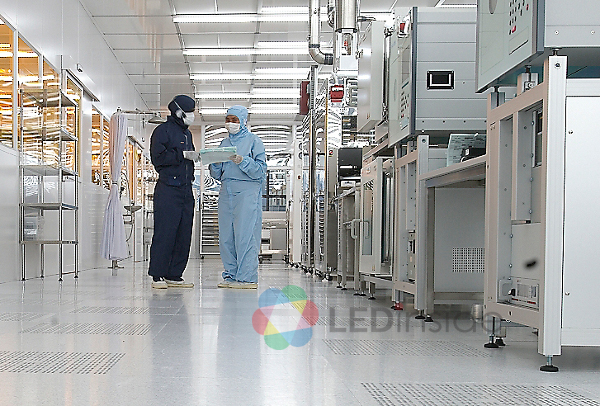
Photo etching room on the left; LED wafer equipment on the right

LED wafer testing equipment in OSRAM Penang base
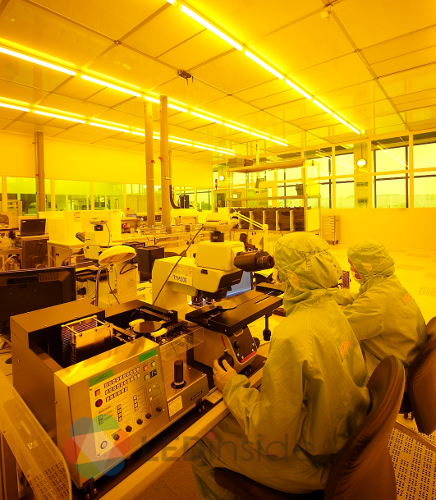
Photo room in Penang base
PEN 31’s manufactures and capacity are upgrading at the moment. PEN 31 plant will introduce 6-inch wafer production as well, although it is still undergoing the testing stage. OSRAM is planning to increase its capacity of LED’s initial production. PEN 32 plant, which is currently under construction, will be in Penang base as well.
According to LEDinside, after PEN 32 plant enters mass production by the end of 2013, Penang base’ LED initial production capacity will be larger (currently the capacity is 2,500 4-inch wafers per week), which will be too much for Penang base’ capacity of LED latter production. Hence, the new LED production base in Wuxi China will be the answer. LEDs that have gone through the initial production stage in Penang will be sent to Wuxi base for the latter stage.
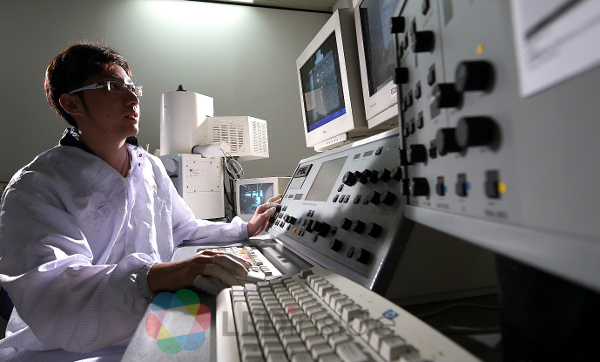
LED wafer production management
LED BE Site in Penang
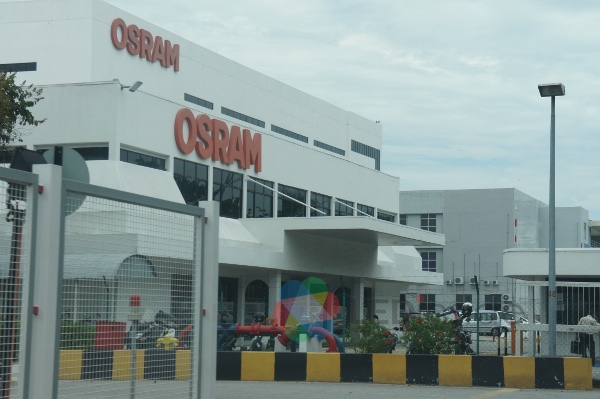
The mission of Penang base is LED packaging and testing, and after Penang base reaches vertical integration, it will be even easier to assure quality. According to LEDinside, OSRAM places a lot of emphasis on package technology, automated testing and visual inspection. OSRAM holds itself to such high standards not only in LED packages with high-efficiency ceramic substrates but also LEDs with SMD packages.
As for Penang’s LED package production, ceramic substrate makes up 10% and SMD 90%. Wuxi base is expected to follow suite.
PEN 1 and PEN 2 plants are in charge of the latter stage of LED production, while PEN 30 focuses on testing, PEN 5 on assembly, testing and R&D of package, PEN 6 on storage, PEN 8 on staff training. All these plants make Penang base a wholesome industrial park for OSRAM’s LED business.
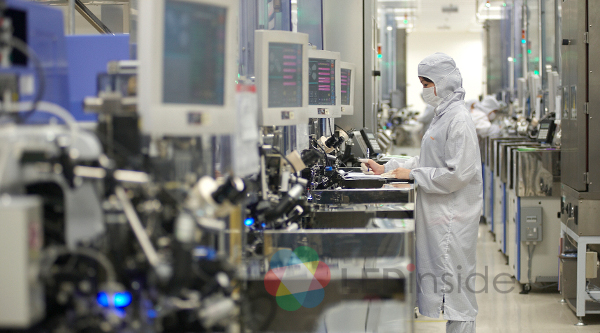
LED wafer testing process in OSRAM Penang base
Through the latter stage of LED production, GaN LEDs will be made into white-light LEDs of different color temperatures with phosphor. In addition, Penang base also handles IR LEDs, optical communication components, automotive LEDs, and Pico Projector.
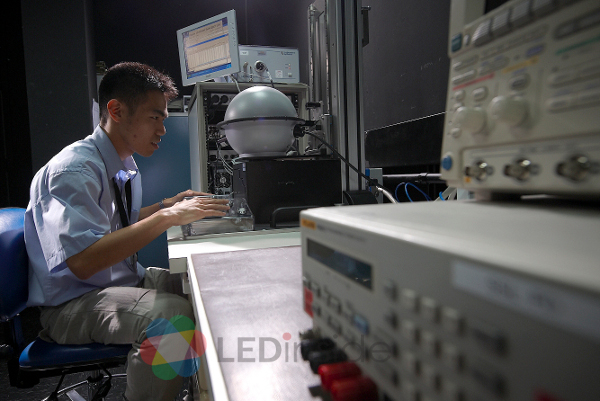
Optical testing process in Penang base
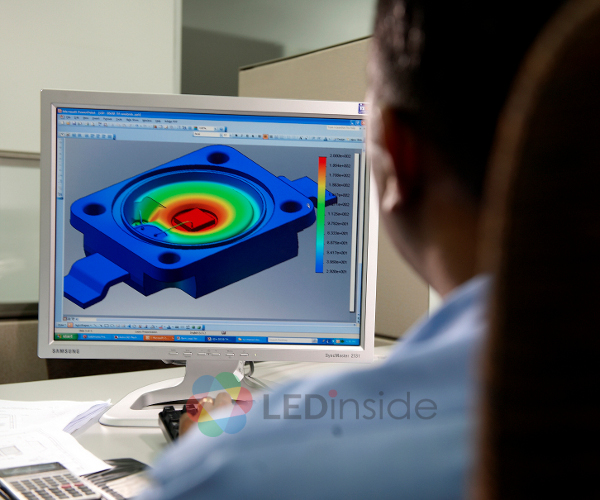
Optical design in Penang base
LED BE Site in Wuxi
OSRAM OS’s Wuxi base construction is schedule to be finished by the end of 2013, which will provide more high-tech job opportunities for the Chinese market.
The reason why OSRAM chose Wuxi is because of its excellent infrastructure and environment. Wuxi already has LED and semiconductor industrial chains and is close to Shanghai and Pearl River Delta market.
Multicultural Working Environment and Team Management Reflects High Quality
During this visit, LEDinside focused most on OSRAM’s management strategy and company culture. The staff consist of Malaysians, Chinese, Indians and people from other countries. Through the English language and a respect for different cultures (they company celebrates holiday from all cultures), OSRAM forms a friendly and multicultural work environment.
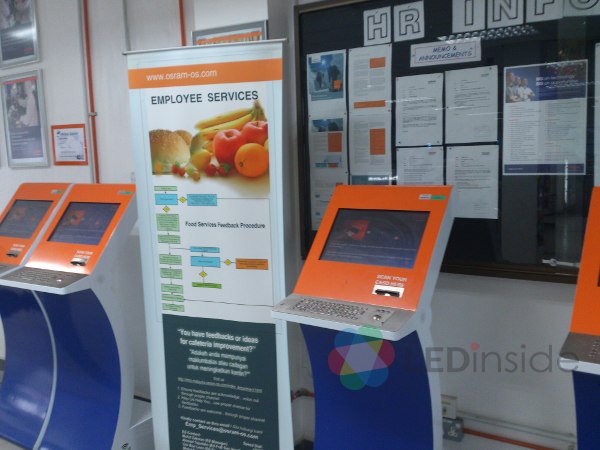
Furthermore, in terms of team management, the company values each and every employee’s sense of honor and growth. At the Penang base, you can see the signs, posters, photos, and activities that represent different teams. A healthy competition between different teams is good, but it is also important to let employees have a sense of allegiance and hold themselves to high standards, which can lead to high product quality. These measures assure excellent quality of OSRAM’s high-end, high-efficiency, high gross profit products and give the company enough resource to continuing developing new technologies. OSRAM has a SOP that has been working smoothly and successfully in Penang base, and now the company is going to take the SOP to Wuxi base. OSRAM will play an even more integral role in the global LED industry.
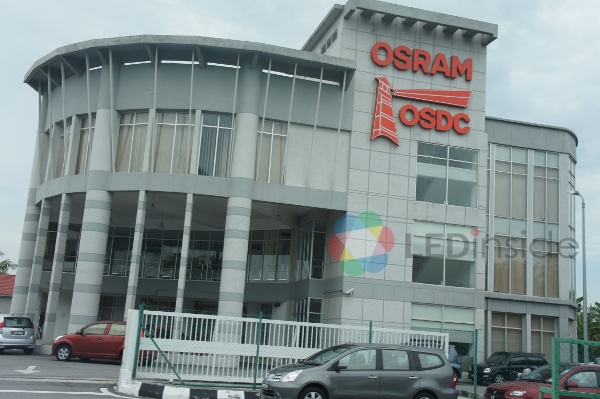
OSRAM Skills Development Centre (OSDC) in Penang, Malaysia, where new employees are trained
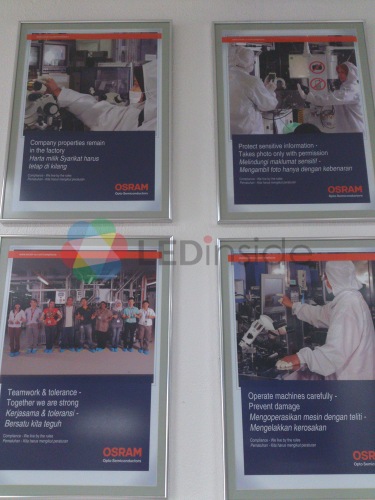
Posters that emphasize the importance of safety in work enviornment