Machine operators at a Bobcat Company manufacturing facility in North Dakota can leave one tool at home now that LED lighting illuminates their work space.
Workers at the Wahpeton plant, located 55 miles south of Bobcat’s corporate headquarters in West Fargo, manufacture hydraulics, cylinders and valves for Bobcat® loaders, compact excavators and attachments. And in this high bay space where welding, assembly and testing are performed, lighting is imperative—and was, at times, supplemented with flashlights. Since GE’s Albeo™ LED high bay lighting replaced 297 metal halide fixtures, the hand-held devices are no longer necessary as lighting levels have nearly doubled.
“When employees started working under the new lighting, they told us, ‘Wow! I can really see better!’” said Brooks Klinnert, an electronics technician with Bobcat who was instrumental in choosing the new lighting. “One operator told us he didn’t even need his flashlight anymore because the new LED lighting provided directional lighting that helped him with his tasks."
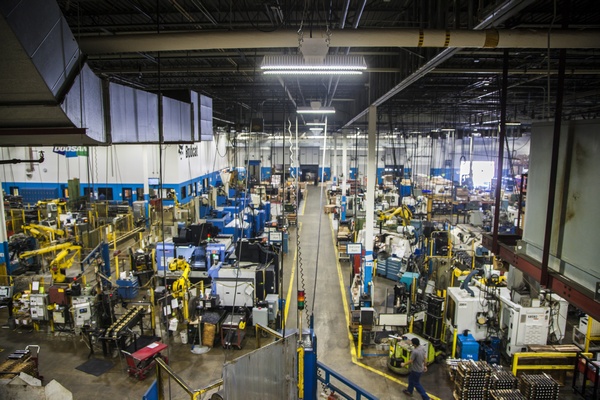 |
Since replacing 297 metal halide fixtures, annual energy costs at this Bobcat® facility have decreased by more than $50,000. (GE/LEDinside) |
The Wahpeton manufacturing facility houses about 98,000 square feet of high bay space that now is illuminated with GE’s Albeo ABH and ALC4 LED high bay lighting fixtures which have reduced energy use by more than 850,000 kilowatt hours (kWh) each year. Annual energy costs have decreased by more than $50,000, and that savings increases when factoring in the diminished maintenance needs—the LED lighting fixtures have a rated lifetime of 100,000 hours compared to a 20,000-hour rated life of metal halides.
“When we began researching new lighting, our goal was to increase light levels and reduce energy usage,” Klinnert said. “We first tested fluorescent lamps, but we noticed issues with the reflectors and had lamp failures, so we started looking into LED. We soon concluded that it was the best lighting technology solution for us.”
Harlan Andersen, Bobcat’s sourcing specialist who oversaw the lighting project, echoed Klinnert’s assessment.
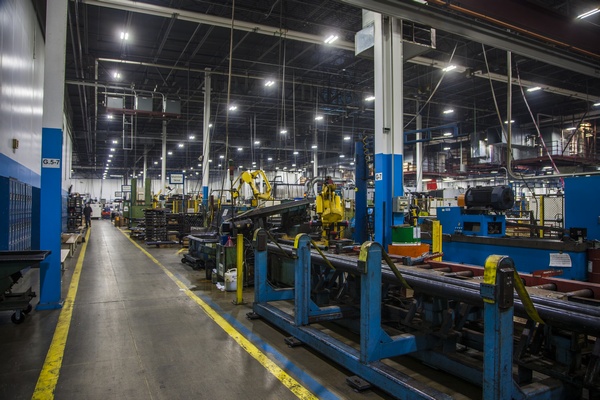 |
Bobcat production line. (GE/LEDinside) |
“Operations at our Wahpeton site are critical to the business, so we wanted to be sure we made the best decision,” he said. “After visiting the other manufacturing facility, we saw firsthand and became confident that an LED lighting solution would be beneficial on many levels.”
The Bobcat team engaged their Grainger representative, Jack French, who knew they were testing several products from a variety of manufacturers. In the search for the right fixture for the facility’s needs, Jack partnered with his local GE representative, Scott Fergen, and helped Bobcat discover that GE’s Albeo LED high bay fixtures produced the best light output, were durable and would help them achieve considerable energy savings. The decision to proceed was solidified after the team visited another manufacturing plant—half of which was lit by Albeo LED lighting and the other half by fluorescent lamps—and “it was a night-and-day comparison. We saw that, and it became a no-brainer,” said Nathan Gemar, a Bobcat indirect sourcing specialist.
In less than two weeks during the plant’s 2013 holiday shutdown, a Moorhead Electric team seamlessly transformed the Wahpeton space from dingy to vibrant, installing 276 Albeo ABH LED luminaires—75 of which are higher output fixtures along the facility’s perimeter—plus nine Albeo ALC4 LED linear fixture s affixed over tall machines. On average, the foot-candle (fc) reading increased from about 22 fc to 40 fc.
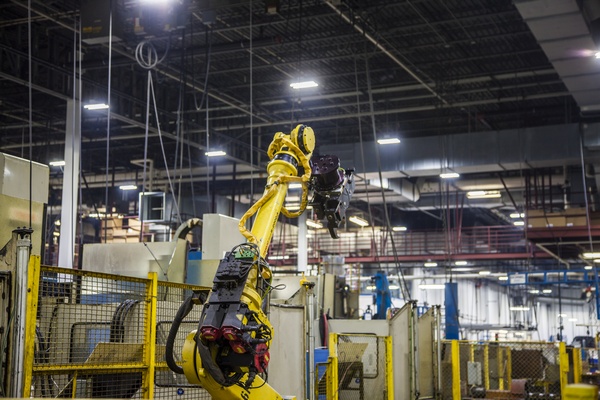 |
Machinery in Bobcat lit up with GE LED lights. |
Midway through the changeout, walking through the Wahpeton plant was like “driving down the road on a cloudy day; being under the new LED lighting was like coming out from under a cloud. It made such a difference and was a drastic change,” Klinnert said.
Gemar said the previous metal halides produced a lot of wasted light and illuminated the ceiling, and the team previously painted the walls so the space would appear brighter. But the new LED focuses lighting where it’s needed, helping employees as they do their jobs—and no longer with a flashlight at the ready.
Doug Krick, Bobcat Company strategic business unit manager, was an early skeptic of the LED solution.
“The first LED lighting was set up in our shipping bay, and I was not sold,” he said. “We had basically taken what we had and replaced them with LED—but the area was not engineered to place the best lighting in the best format.
“The team then placed a sample in an area engineered for the best lighting performance in savings and candle power. LED proved to be the best option with lower maintenance costs as well as the best candle power. I had been a skeptic, but the team proved LED was the best option. I let the data show me the way.”
“I was extremely pleased with the outcome at the Bobcat plant,” French said. “This is the perfect example of leveraging Grainger’s Core Value Proposition of taking cost out of our customer’s business!”
To learn more about GE’s LED lighting solutions for industrial facilities, visit www.gelighting.com/industrial.