The LED industry is gradually maturing in 2015, with products cost/performance (C/P) ratio becoming increasingly important. Low and mid-power flip chip products are increasingly valued by the industry. To further understand this trend LEDinside recently interviewed Lattice Power Chief Technology Officer Hanmin Zhao.
Low and mid-power flip chips solve die bonding challenges
Mainstream LED chip package types in the LED industry can be categorized into Surface Mount LED (SMD), Chip On Board (COB) and ceramic. Package materials can be classified into Epoxy Molding Compounds (EMC), polyphthalamide (PPA), PPT, metal-Printed Circuit Board (PCB) and ceramic. LED package manufacturers die bonding methods often varies and depends on the substrate and package materials. Most LED package manufacturers are using clear adhesives, solder paste, or silver adhesives in low or mid-power LED applications. In contrast, manufacturers are using eutectic die bonding for high power LEDs. To meet these different die bonding demands in flip chip products, Lattice Power flip chip products can be separated into high power and low to mid-power LED chips. Among the two different power LED chips, the similarities between two types of chip designs is approximately 80% to 90%. Gold-zinc pads makes it easier for eutectic die bonding in mid to high power LED chips for clients. In low to mid power LED applications, there is an especially designed passivation layer. This ensures the chip does not short circuit, if the solder paste is of really bad quality. The company’s strategy is aimed at improving yield rates of products ranging from low to high power LED products, while providing the products with high reliability, convenience, and lowering costs.
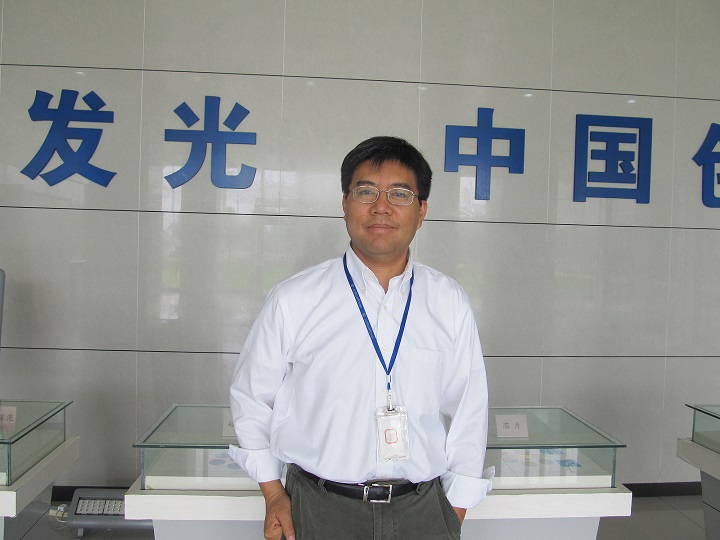 |
Lattice Power Chief Technology Officer Hanmin Zhao. (Lattice Power/LEDinside) |
Lattice Power was one of the earliest LED manufacturers in China to develop flip chip LEDs, said Zhao. Performance of the company’s flip chip products is on par with leading international LED manufacturers. LED color temperatures of its flip chip products have reached 5500K, CRI 70 and white light 45 mil. The company’s chip package component luminous efficacy reached 160 lm/W when driven at 350 mA.
Advantages of using eutectic die bonding for high power LED flip chip applications is becoming increasingly evident. When ceramic packages are used in flip chip applications, there are no coefficients of thermal expansion (CTE) mismatch issues. Additionally, ceramic packaged flip chips performance often outshines high power LEDs, while there has been little improvement in the small to mid-power LED market. Responding to this market trend, Zhao noted surface mount packaging for small to mid-power flip chips is still in the R&D phase, and there are still CTE mismatch issues that needs to be solved.
Although, flip chips have many advantages including good thermal dissipation, electric conductivity, does not require wire bonding, is highly reliable, and is small in size. In the next few years, it will be possible that a large portion of the products will be used to replace traditional flip chips. Lattice Power has observed these market trends, and is vying after this particular market. Lattice Power has developed SMD and COB packaged mid power LED chips and ceramic packages suitable for high power flip chip LEDs and other new products.
Pros and cons of CSP
Chip Scale Packaging (CSP) is a completely new concept in the LED industry, but the IC industry has been very familiar with this technology for years. CSP will play an increasingly important role in the LED industry, and similar to IC products CSP will not be replacing all LED products in the industry.
CSP will become an increasingly important player in the LED industry. CSP technology has reduced and even gotten rid of leadframes, hence lowering costs, said Zhao. Additional features and advantages include improved lighting patterns and better thermal dissipation features. Even though CSP technology can be very attractive for many types of applications, the resulting LED chip can be more fragile than conventional SMD packages. CSP LEDs ultra-small chip size, high precision demands for surface mounting equipments, and lack of leadframes can make its chip structure more fragile than traditional LED chips. This is why in certain lighting application sectors CSP has progressed rapidly, but is slower in other market sectors.
In CSP LED developments, Lattice Power has built upon its 6-inch GaN substrate technology to develop GaN-based CSP technology. The company aims to complete related technology developments within a year, and introduce it into the market.
The ultimate LED product might be GaN-based flip chip films, said Zhao. Lattice Power’s current flip chip production capacity is about 30,000 LED chips per month. Following the rising flip chip market, Lattice Power is prepared to expand production capacity, and readying itself ahead of mass scale flip chip production.
GaN-based LED substrate has always been an ideal technology, but it has been difficult to overcome technology barriers, said Zhao. Hence, many manufacturers are turning towards sapphire substrate and GaN-on-Si technology. Lattice Power, for example, started mass production of low-power GaN-on-Si LED chips in 2009. By 2012, the company was manufacturing high power GaN-on-Si LED chips, and commercializing GaN-on-Si LEDs.
Compared to sapphire substrates, GaN-on-Si substrate LED technology advantages in high power LED chips and large sized LED wafers will become increasingly evident. Lattice Power’s next step will be developing GaN-on-Si flip chips to ultimately achieve “flip chip film”—which will realize the advantages of flip chip, and emit light on a single side of the chip.
Lattice Power has been diligently developing and manufacturing GaN LED technology. Whether it is sapphire substrate or GaN substrate technologies, manufacturers need to see whether these fit their development strategy. From the client perspective, their choice will depend on consumer demands
(Author: Skavy Cheng, Editor, LEDinsidehttp:// Translator: Judy Lin, Chief Editor, LEDinside)