Smart manufacturing will be the key to upgrading the printed circuit board industry! ITRI exhibited its expertise in innovative PCB manufacturing technology at the TPCA Show 2016, displaying the High Aspect Ratio Maskless Fine Line Printing Technology and Additive Process for Printed Fine Line Circuits, as well as its Intelligent Power Module for Automotive Battery Control. ITRI's innovative technology will assist in propelling the value of both the upstream and downstream sectors of Taiwan's PCB industry, thereby solidifying the foundation in making the industry a trillion dollar one in the future.
Dr. Chih-I Wu, ITRI's Vice President and General Director of Electronic and Optoelectronic System Research Laboratories, remarked that unlike the past when electronic products featured standardized specifications, the focus today is more towards flexible and customized production. This trend of producing limited quantities of a variety of products is forcing Taiwan's PCB industry to emphasize smart manufacturing, which will enable companies to satisfy the demands of customers efficiently. In light of this, ITRI is making every effort to provide the PCB supply chain with technology to enable them to move from "automated" to "smart" manufacturing.
Dr. Wu further stressed that roll-to-roll (R2R) fine line technology, an additive manufacturing method to replace photolithography, constitutes a technological breakthrough for ITRI. In tandem with ITRI's Self-guided Additive Manufacturing for Minimum Carbon Emission with Roll-to-roll Production Systems (SAMMCERS), a finalist for 2016 R&D 100 Awards, the R2R process can achieve low-carbon and smart manufacturing. Meanwhile, ITRI's UHF Systems Laboratory, which is state-of-the-art in Taiwan, creates an R&D environment for the design, measurement, and validation of UHF millimeter wave systems, offering a comprehensive capacity to test circuit boards. This will be conducive to providing the PCB industry solutions amid the need for fine line and high frequency/speed products.
The key achievements displayed by ITRI at this year's show include:
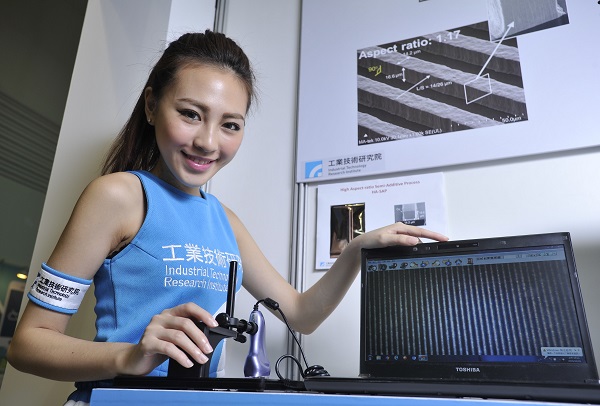
|
ITRI and SERIA jointly developed the High Aspect Ratio Maskless Fine Line Printing Technology. (All photos courtesy of ITRI)
|
●High Aspect Ratio Maskless Fine Line Printing Technology
ITRI and SERIA, a major printing factory in Japan, jointly exhibit the High Aspect Ratio Semi-Additive Process (HA-SAP). With an aspect ratio larger than 1:1, this technology combines the advantages of rapid printing with mass production grade and high quality fine line circuits. The verticality of the copper wire along the side can reach nearly 90 degrees, which offers higher current loading and easier adapting to circuit design to fulfill high density circuit demand. Furthermore, HA-SAP can help reduce the high capital expenditures associated with exposure equipment, which will effectively boost the competitiveness of the PCB industry. Combined with ITRI's SAMMCERS, HA-SAP can achieve the goal of creating a smart production line. When the designated ideal parameters have been exceeded, SAMMCERS will immediately detect the issue and make prediction to determine whether quality is being compromised. If appropriate, SAMMCERS will amend the parameters and recalibrate the system. Under this mechanism, quality stability will be enhanced in production while reducing carbon emissions by 50%.
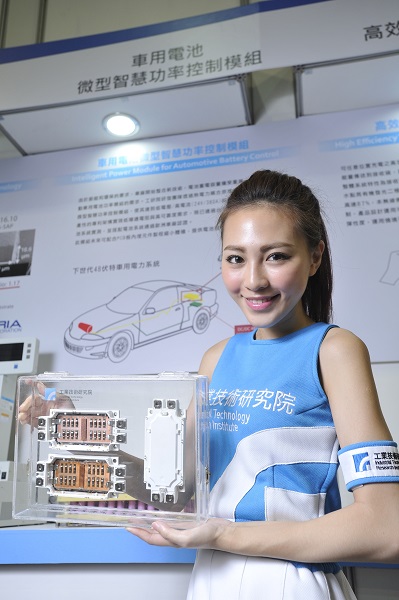 |
ITRI exhibits Intelligent Power Module for Automotive Battery Control at the TPCA show.
|
●Intelligent Power Module for Automotive Battery Control
ITRI developed a platform with thermal, electrical and stress co-simulation to evaluate intelligent power control module design for car batteries. The module can thus meet the low voltage/high current (24V/380A) modular specification and achieve low Drain-Source On-Resistance (Rds(on)) for vehicle reliability requirements. ITRI also applied a new module structure patent to realize the product ideal. Moreover, the module has passed the function test of battery system from Taiwan's car battery manufacturers. The test results meet the temperature rise range under long time and high current operation. In the future, the intelligent power control module can be miniaturized with embedded PCB components and provide high performance for automotive battery systems.
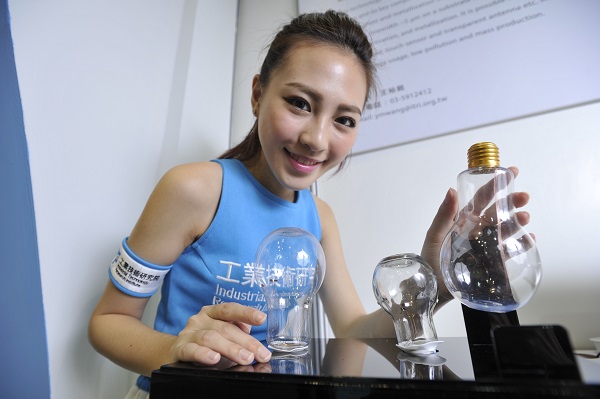 |
ITRI’s Additive Process for Printed Fine Line Circuits enables printing with line width of under 5 μm.
|
●Additive Process for Printed Fine Line Circuits
ITRI's Additive Process for Printed Fine Line Circuits involves special materials, innovative printing equipment, and gravure offset printing technology. Breakthroughs enable high resolution printing of patterns with line width of under 5 µm. Even more important is that this eco-friendly manufacturing technology can reduce the maximum by over 80% the amount of materials used and by over 60% the power consumption. At the same time, this technology can be applied to curved glass and PET plastics. Circuits will be able to be printed directly on dashboards or on curvatures in robotic arms used on production lines. This development will effectively expand the range of uses and possibilities in circuit design. Presently, ITRI and Career Technology (Mfg.) Co., Ltd. are collaborating on FPC production for smartphone and tablet computer touch modules.
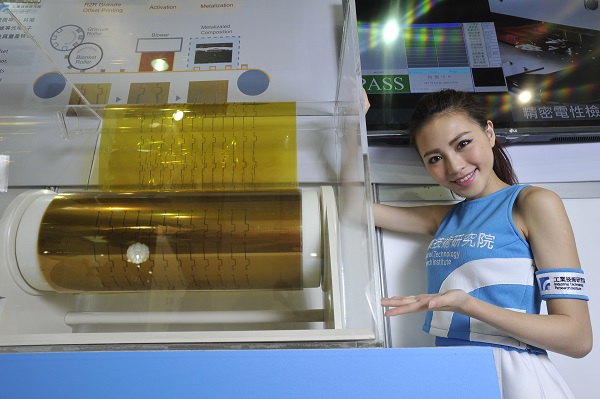 |
ITRI’s Additive Process for Printed Fine Line Circuits enables printing with line width of under 5 μm.
|
● PCB Equipment Communication Software
Production line machinery currently used by Taiwan's PCB makers features a variety of none-standard communication interfaces. In response to the challenges in manufacturing data collection, ITRI has developed PCB equipment communication software that establishes effective communication between the host and PCB equipment and complies with SEMI E4/E5/E37/E30 standards to ensure high reliability. The software solution can be adopted in the semiconductor, LED, LCD, and other industries. In addition, ITRI and the Taiwan Printed Circuit Association are working together on drafting a PCB equipment communications standard. The common standard for the PCB equipment in Taiwan will facilitate the development of information gathering and analysis platform for PCB production lines. This will thus improve production data management, which can enable fault diagnostics, real-time monitoring, machine-to-machine communication, and other smart manufacturing practices.