Laser micromachining specialist has developed a proprietary side-wiring technology that offers low-resistance wrap-around wires for seamlessly tiled displays
Hsinchu, Taiwan: Bolite Co., Ltd., a laser micromachining subsystem and equipment manufacturer, today announced the Bolite SW-L laser-based, automated side-wiring system, which provides wrap-around wires on the sides of the display panels to connect Micro LEDs to the drive ICs. Supporting various panel sizes and featuring high-precision alignment, advanced process control, and full automation with robotic handling, the multi-functional Bolite SW-L will help display manufacturers to accelerate the commercialization of large, seamlessly tiled Micro LED displays while meeting the volume manufacturing needs for other thin-bezel display applications.
Panel-tiling and Bezel-less borders Driving Side-wiring Needs
Micro LED has the potential to be considered as the ultimate next-generation display technology due to benefits such as high dynamic range, brightness, and low power consumption. Currently, smaller Micro LED panels (up to 17-inches) are manufactured first then tiled to produce displays as large as a whole wall. To achieve high-resolution displays with small pixel pitches, minimal edge or bezel width is highly desirable. While flexible PCBs or through glass vias (TGV) can be used to connect the Micro LEDs to the drive ICs, side-wiring is another attractive solution to complete the electrical connections.
“The display industry has increasingly demanded a solution to address panel-tiling and the ever-shrinking bezels,” said Dr. Bowen Cheng, General Manager of Bolite, “After more than a year of intensive development and close collaborations with several key partners, we are proud to introduce the Bolite SW-L laser side-wiring system. It represents a major breakthrough in facilitating the seamless tiling of Micro LED panels. In addition to producing low resistance side wires at high speeds, the Bolite SW-L has an integrated laser grinding module to precisely chamfer the corners of the glass substrates, which helps to improve the continuity and reliability of the metal wires. I am also pleased to report we are in the process of delivering this tool to a major display manufacturer.”
Key equipment features & benefits of the Bolite SW-L include:
• Precision laser patterned, low resistance side-wires on sputtered metals with no photolithography masks.
• Front and backside direct laser patterning of electrodes, leads, and fan-outs.
• Laser grinding for glass side profile treatment improves alignment accuracy and minimizes the edge damage of other processing techniques such as mechanical grinding. The chamfered edges increase the edge strength of the tiles and improve the continuity and reliability of the metal wires.
• Cost-effective and high-throughput potential: up to 2,000 panels per month.
• Line/Space: 20 µm/20 µm (typical); 5 µm/5 µm (minimum, depending on substrate edge quality).
• Wire Resistance: < 10 Ω.
• Alignment Tolerance: ± 10%.
• Highly compatible with the TFT manufacturing process.
Product Availability
Bolite is now accepting orders for the new Bolite SW-L side-wiring system. In addition, the company is offering product demonstrations at Bolite’s Laser Application and Demo Center at its headquarters in Taiwan.
Limited quantities of reference samples are also available upon request.
For more information on Bolite Co., Ltd., please visit www.boliteopto.com.
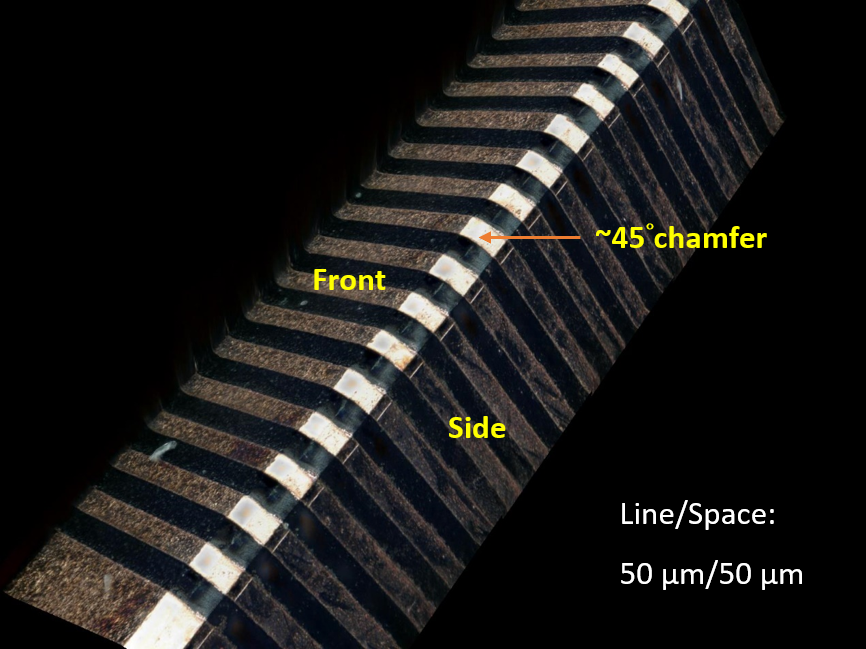
Figure 1. Laser patterned side wires.
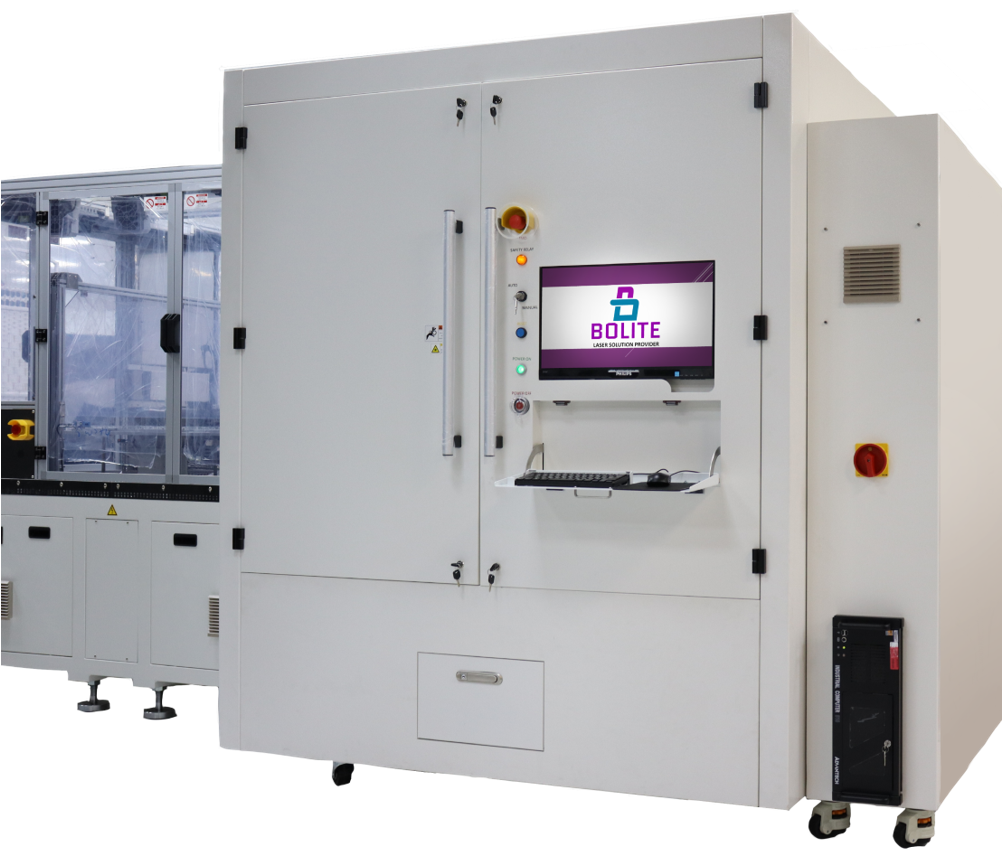
Figure 2. Bolite SW-L side-wiring system.
2022 Micro LED Self-Emissive Display Trends and Analysis on Suppliers’ Strategies
Release Date: 31 May 2022 / 30 November 2022
Language: Traditional Chinese / English
Format: PDF
If you would like to know more details , please contact:
|