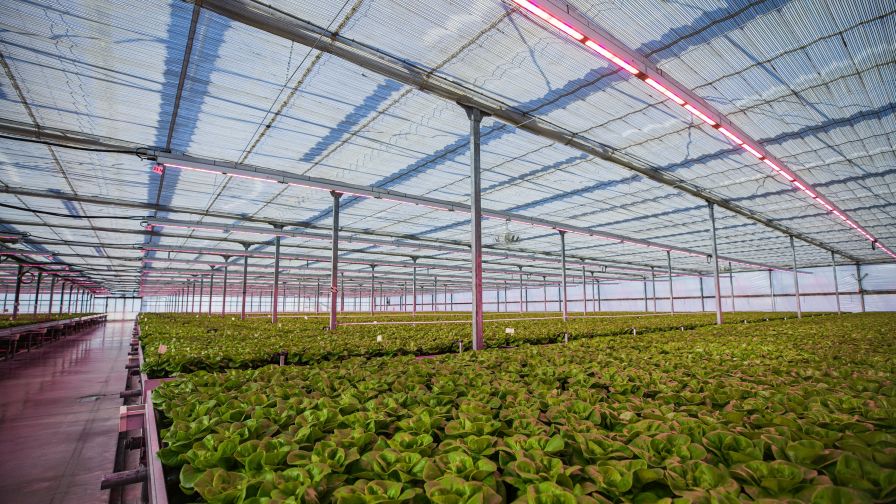
Lights that respond to current conditions eliminate the need for continuous grower input, simplifying the process and letting growers focus on growing, not on spending time in front of the computer. Photo: Signify
LED lighting has come quite a long way in the past few years. What began as a simple energy-efficient replacement for high-pressure sodium (HPS) legacy systems has become a customizable solution to better yields, faster cycle times, and even higher energy efficiency. While work is still being done to improve the efficiency of turning electricity into photons, that’s not the only area where new lighting technology is coming to bear.
Technologies that weren’t cost-effective a few years ago, like dynamic spectrum control, are now going mainstream. Old-school on/off lighting systems are also being improved.
“The biggest, or the most common, pain point is the grower’s lack of flexibility and control over their lighting,” says Matthew Bonavita, Senior Sales Director – U.S. market for Sollum Technologies. Legacy systems, even older LED systems, don’t adapt or adjust to the needs of the crops or different crop cycles. “It leads to inefficiencies, lower yields, higher energy cost,” he says.
Intelligent Dimming and Spectrum Control
While it doesn’t make sense in every situation, dimmable LED lighting can be a fantastic energy saver. Smart controllers can adjust the power output, and thus the light output and energy consumption, of dimmable LED fixtures throughout the day without input from the grower.
New systems are more integrated with other greenhouse controllers and sensors.
“Our Grow Wise control system is a proprietary dimming technology, a software and interfacing tool. It’s essentially a small local area network that connects to the climate computer. It can respond to inputs that it reads from climate computer software,” says Colin Brice, Sales Application Specialist – Horticulture LED Solutions at Signify (formerly Philips Lighting).
Lights that respond to current conditions eliminate the need for continuous grower input, simplifying the process and letting growers focus on growing, not on spending time in front of the computer.
New advances in wireless technology are also being utilized in lighting control. Long wiring runs to reach fixtures farther from the controller present issues due to voltage drop, and signals can’t be run independently to each fixture in the bank. With wireless signals for dimming, both problems are solved. Lights on a bank can be controlled for color and intensity, establishing multiple zones even within the same bay without running new wiring.
“A lot of growers want control on a much more discrete level. For example, if I’m moving a lettuce crop across a greenhouse on mobile gutters, and I want to put more blue light at the end of the cycle to have better coloration on my lettuce, but I don’t want to put more blue light at the first part of the cycle because it’s less energy efficient,” Brice explains.
High fidelity in dimming control works well with a DLI (daily light integral) controller. The controller uses sensors to measure real-time light, and the LEDs can be dimmed or powered up as required, depending on the amount of light the crop needs.
“Our algorithm is looking at different factors to help minimize energy consumption. One of them is actually looking at the efficacy of the light. We’re also integrating energy prices to avoid peak rate hours throughout the day,” explains Rebecca Norden, Chief Commercial Officer at Heliospectra. “Today growers can reach really high energy savings compared to previous systems. Using the DLI mentioned system, you can save another 35%, especially in the shoulder months, in autumn and the spring.”
“Growers can adjust the lights based upon a sunny or cloudy day. Having that control not only maximizes yield, but also reduces energy consumption. It provides the plants with the right light at the right time,” Bonavita says.
High-Powered Fixtures and Lens Technology
Not only is efficiency rising, but so is power. Higher wattage power supplies and improved optics are increasing light uniformity and the coverage footprint per fixture. Fewer fixtures mean lower installation costs and fewer cable runs. Wide beam lighting advances mean improved uniformity over the crop, sometimes reaching 90%.
Central power supplies are becoming more common, allowing for greater flexibility and potentially reduced installation costs. Running multiple modules off one power supply has advantages.
“The new trend with power supplies is an increase in the power supply wattage. Growers want to have more µmo/m2 (micromoles per square meter), so the PPFD will increase,” says Bonny Heeren, CEO of Heliospectra.
You might think a light-emitting diode is just a diode with little room for improvement, but that’s not true. New products on the market are using larger diodes for better efficiency. “To make the LED itself more efficient, the footprint of the diodes becomes bigger,” Heeren says. For the same-size light fixture, there are fewer diodes, but the light output remains the same.
Specialized Knowledge and Support
When growers started shifting to LED lights, they were basically just a more energy-efficient way to provide supplemental lighting while reducing the electric bill. In the “old days,” there wasn’t a vast body of research, practical application knowledge, case studies, and experience about how to best use new LED lighting. Now there is.
The industry has troves of data to work with, from custom lighting recipes for individual crops to adding white for worker comfort, or even changing the lighting for different propagation stages.
Future Trends and Emerging Technologies
What’s coming soon? Expect more integration between the greenhouse lighting controllers and sensors, steered in real time. Combining dimmable, spectrum-controllable LEDs with sensors in the crops and smart controllers that integrate the sensor data, weather forecasts, energy prices, and more will yield further savings and provide an even more precision-managed crop.
But new, discretely controllable lighting has other benefits too, especially for greenhouse workers. The ability to create multiple zones and recreate them as needed allows better management of not only plants but worker conditions as well.
“When you have people working in the greenhouse to harvest the crop, you can add some white light. In the old days, it was 95% red and 5% blue. You get a purple color in the greenhouse, and people get really disorientated. Now, (with dynamic spectrum control) we can increase the white temporarily for that area, so people have better working conditions. It also enables pollination by bumblebees, which is critical in the cultivation of many crops, for example, tomatoes and strawberries,” Heeren says.
TrendForce 2024 Global LED Lighting Market Analysis
Release Date: 01 February 2024 / 31 July 2024
Language: Traditional Chinese / English
Format: PDF and Excel
Page: 90-100 / Semi-Annual
If you would like to know more details , please contact:
|