Leading LED chip industry experts had very different perspectives on GaN LED substrates at 2015 LED Executive Summit hosted by SEMI at TILS 2015 in TWTC Nangang Exhibition Hall, Taipei, Taiwan recently.
Some LED vendors have turned to GaN-on-Si LED technology over recent years to reduce manufacturing costs, since silicon substrates are cheaper compared to sapphire. Leading LED manufacturers turning to alternative substrates include Soraa with its GaN-on-GaN technology, and GaN-on-Si manufacturers Toshiba and Samsung. Yet, Cree and Lumileds speakers pointed out the technology remained far too costly to manufacture economically on a large scale.
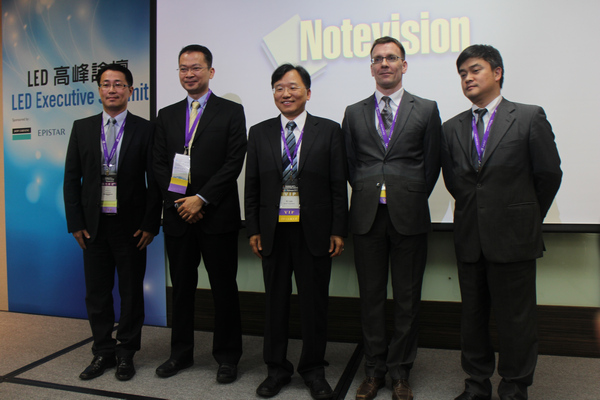 |
Left to right: Yun-Li Lee, CEO, PlayNitride; Walter Chen, General Manager of Marketing, APAC, Cree; B. J. Lee, Chairman, Epistar; Michael Schmitt, APAC Marketing Director, SSL, Osram; Sean Zhou, Marketing Director, Asia Regional, Philips Lumileds. (LEDinside) |
In theory, silicon wafers are cheaper than sapphire and projected to help manufacturers save 1 cent per square millimeter (mm2), said Sean Zhou, Marketing Director, Asia Regional, Philips. Silicon have a much larger size of above 200 mm, sapphires at most measure 150 mm, while the largest GaN wafer is only 50 mm.
Moreover, for every 15% lower EPI efficacy in silicon, about double EPI area is required compared to sapphire to meet the same lm/W. In reality, GaN-on-Si LEDs have a 10% performance gap, and in general a 66% higher EPI than sapphire.
Silicon also has a poor lattice constant compared to sapphire, said Zhou. Silicon has a lattice constant of 3.84 compared to GaN’s 3.19A, while sapphire has a slightly closer match of 2.75, said Zhou. GaN-on-Si’s cost ineffectiveness was echoed by Walter Chen, General Manager of Marketing, APAC, Cree, who also agreed it was not cost effective.
In general, sapphire has the best lattice constant when matched with GaN, followed by silicon carbide (SiC), while silicon wafer trails last. Due to the poor lattice constant match, even if manufacturers could save 10% on silicon wafer material, companies often will need to spend more effort on epitaxy growth, said Chen. The lower yield rates have actually made GaN-on-Si LEDs a net cost adder, explained Zhou.
GaN-on-GaN LEDs are also very expensive to manufacture because of the smaller wafer size. Zhou projected GaN wafer prices will remain high in the next five years. In contrast, sapphire prices have declined significantly over the last five years, he added.
In short, GaN-on-GaN LED or GaN-on-Si is not always cost effective, and it may take several years before GaN or silicon substrate based LEDs can match current LEDs.
(Author: Judy Lin, Chief Editor, LEDinside)
(Editorial note: The headline of this article was changed on April 4, 2015 to better reflect article content. Other edits were also made to better reflect different views on LED substrate materials in the industry, instead of using the term GaN LED.)