Costs. That is the only thing LED chip manufacturers think about, and who can blame them? LED chip prices are expected to drop to 50 cents for a 1,000 lumen LED lamps in 2015, said Epistar Chairman B.J. Lee at 2015 LED Executive Summit hosted by SEMI at TILS 2015 in TWTC Nangang Exhibition Hall, Taipei, Taiwan. Moreover, manufacturers might be facing the challenge of raising LED efficacy to 3,000 lm/$ within two years. Tightening profits are spurring manufacturers to develop new technology to drive down costs.
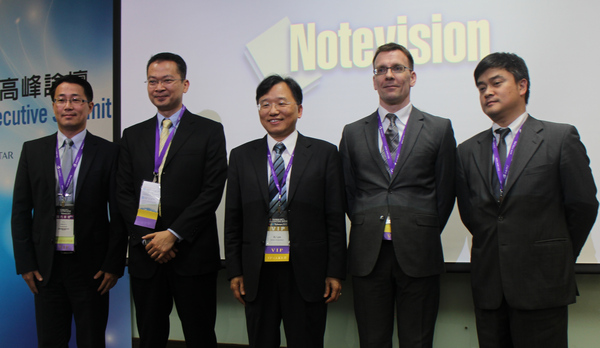 |
Left to right: Yun-Li Lee, CEO, PlayNitride; Walter Chen, General Manager of Marketing, APAC, Cree; B. J. Lee, Chairman, Epistar; Michael Schmitt, APAC Marketing Director, SSL, Osram; Sean Zhou, Marketing Director, Asia Regional, Philips Lumileds. (LEDinside) |
LED chip manufacturers highlight CSP technology
In general, LEDs make up 30% costs in a LED luminaire, while the remaining 70% costs are from other LED components, such as LED drivers and optic lenses, said Walter Chen, General Manager of Marketing, APAC, Cree. One method of approach is to tackle luminaire costs at a system level, such as reducing PCB, and using less optics, or in the case of Cree developing LED modules to meet market demands. However, most speakers at the forum addressed Chip Scale Package (CSP) technology, which has become widely adopted in the industry to drive down manufacturing costs.
CSP can reduce costs by eliminating the need for ceramic sub mount, while enabling the AuSn or SAC to solder directly on a L2 board, said Sean Zhou, Marketing Director, Asia Regional, Philips Lumileds. Hence, the technology enables cost effective small devices, due to die level processing.
The technology does have certain limitations, though. For instance maintaining package, solder, LED junction and phosphor below reliable operating temperatures. Efficiency limits also exist when meeting system lm/W targets, noted Zhou.
In addition, electrostatic discharge (ESD) cannot be added into the chip in wafer level packaging, and there can be outgassing issues where overflowing sulfur material affects the chip’s brightness, said Chen. Wafer level package has its merits in certain applications, such as high lumen per watt applications, but it is not always suitable for general lighting products, he added.
Epistar focuses on flip chips, Osram experiments with microrods
Clients higher thermal requirements of above 100 degrees Celsius has also led to the rise of Epoxy Molding Compound (EMC) or SMC material in LEDs, noted Epistar Chairman B.J. Lee. EMC is capable of sustaining a junction temperature of 130 degrees Celsius because of its better heat dissipation, which allows it to run on higher temperatures. The design of the chip can either be CSP phosphor on die, or flip chip and phosphor. It can be placed on top of carrier, or even without a carrier. Ceramic substrate, metal or other materials can also be used along with EMC. The material has been used by Lumileds in certain LED streetlight applications, said Lee.
The advantages of CSP white chip design is it can drive higher currents and at higher flux. As flip chip decreases in size, currently some white chips measure 1.3 x 1.3 mm and are only 150 micron thick, there can be new LED applications, said Lee. Other emerging flip chip designs include flip chip on board, where 25 to 50 LEDs are packaged using wire bonding or without handling, said Lee.
Osram has started pilot project of making 3D LED chip structures from InGaN/ GaN microrods, which can enable 10 times bigger chip size, said Michael Schmitt, APAC Marketing Director, SSL, Osram. The new microrod LED technology, which was revealed by Schmitt in late 2014 at LEDforum, will not be entering mass production for the next two to three years, he added.
(Author: Judy Lin, Chief Editor, LEDinside)