VCSEL applications including distance sensing, autofocus, 3D sensing and more have been increasing in recent years with rising demand for facial recognition technology in smartphones as well as ADAS technologies in driverless vehicles.
To strengthen VCSEL development, chip producers and equipment providers are improving their techniques to offer advanced technologies to achieve next generation applications. Veeco Instruments, the US-based semiconductor equipment manufacturer with proven successes in industries such as data storage and LED to help customers reach massive scale, is leveraging its core strengths in engineering and manufacturing to enable the same for next-generation technologies such as VCSELs.
LEDinside interviewed Mark McKee, Director of MOCVD Marketing at Veeco Instruments to further understand the company’s strategies and capabilities in accelerating VCSEL technology development.
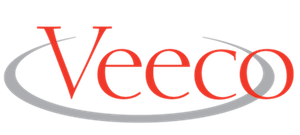
Veeco Provides Cost-effective Solutions for VCSEL Production
To drive cost-effective production of VCSELs, companies need technology that can easily scale while solving these high-value problems. From a deposition technology perspective, McKee indicated that the key requirements are uniform and laminar flow of the metal-organics and hydrides over the surface of the wafers, uniform and controllable temperature and sharp interfaces between layers. Moreover, to achieve highest productivity, MOCVD platforms require longer time between preventative maintenance cycles, fast recovery after preventative maintenance and fast epitaxial growth rates. Veeco has consistently delivered demonstrated performance that help customers achieve maximum productivity.
With increasing higher-power applications (over 100mW devices emitting around 980nm), requirements for VCSELs become more challenging. Equipment providers nowadays have to ensure a high yield for total wavelength population in 6nm bin and composition uniformity for aperture size control. Equipment providers must also grapple with low defectivity requirements (<1/cm2) for structured light and large-area VCSELs, as well as the migration from 4 to 6 inch wafers.
In order to meet the demands, Veeco optimized its TurboDisc® MOCVD technology which delivers the tight requirements needed for more demanding applications like LiDAR in adaptive driver-assistance systems (ADAS) for vehicles and advanced smartphones. Veeco’s TurboDisc roadmap depicts the path device makers need to meet the tight requirements like oxide layer compositional control and Fabry–Perot (FP) wavelength uniformity.
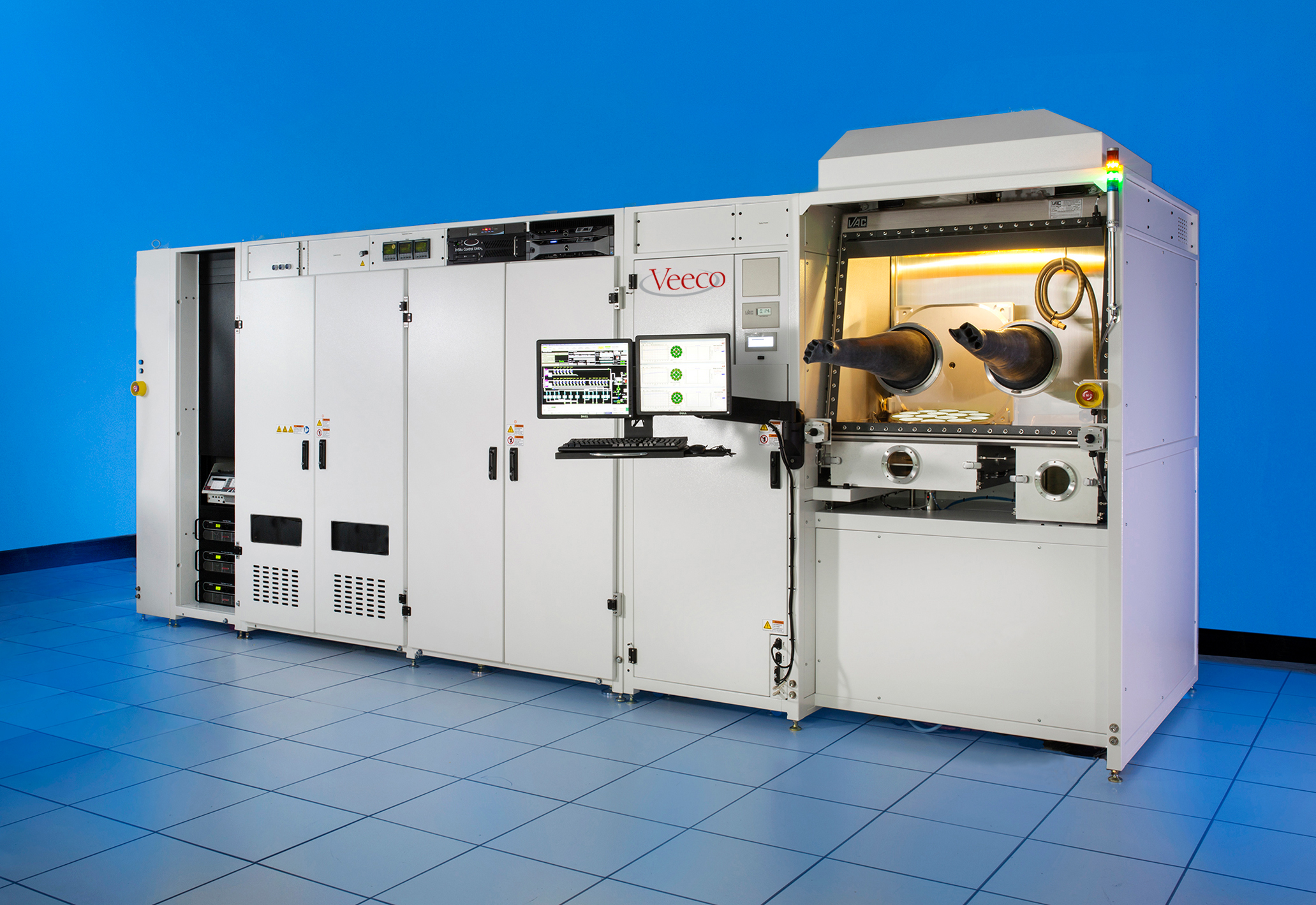
(Image: Veeco)
According to McKee, the TurboDisc MOCVD solution is able to offer higher uniformity and improved within-wafer and wafer-to-wafer repeatability over current industry baseline, combined with the industry’s lowest defectivity. The design of Veeco’s Uniform FlowFlange™ technology provides higher growth rates, ease-of-tuning for fast process optimization and fast tool recovery time after maintenance resulting in 30-50% higher productivity over current VCSEL production toolsets.
Veeco Joins VCSEL Supply Chain and Cooperates with Industry Leaders to Push Technology Innovation
VCSEL technology was originally used for optical communication in the data and telecom space. The technology suddenly became a hit when Apple used it in smartphones for facial recognition. The application in ADAS for the rising self-driving technologies makes VCSEL even more popular. As a result, the VCSEL market is expected to grow significantly in the coming years.
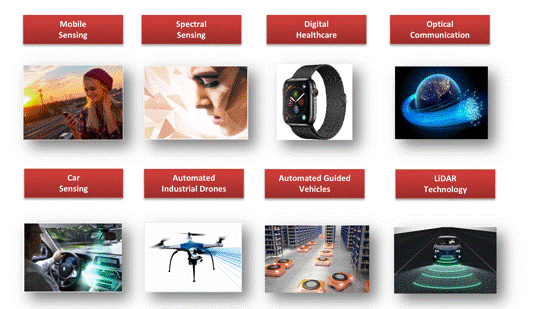
With its TurboDisc technology, Veeco has teamed up with several clients including VCSEL manufacturers and research institutes for developing technologies required for applications such as AR/VR devices, smartphones and LiDAR. In addition, Veeco also supplies metal lift-off (MLO) technology for several first-movers in the VCSEL supply chain through its ImmJET™ immersion and single-wafer wet process technology. These wet processing systems are the process tool of record (PTOR) for MLO and etch in VCSEL production with leading customers today.
To further expand the implementation of VCSELs, Veeco has worked strategically with its clients to provide optimal performance, high yield and tool productivity, keeping up with the demand associated with increasingly innovative applications that are poised to capitalize on the advantages of VCSEL technology.