(Author:Judy Lin, Chief Editor, LEDinside)
Founded three years ago, Idaho-based Rohinni is eyeing different segments in the micro-LED application sector with a LED die based manufacturing process: the first industries they have targeted will be keyboard backlight, logo and the automotive lighting sector.
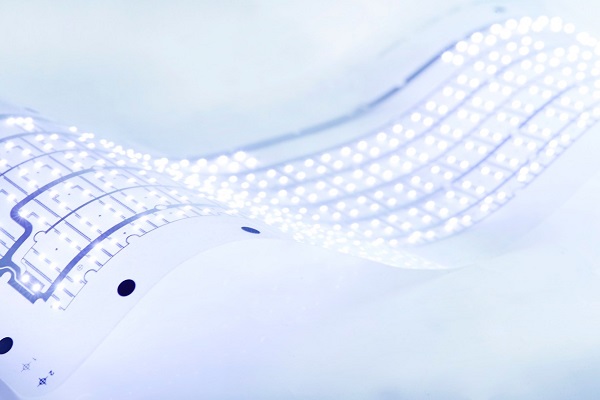 |
Rohinni's micro-LEDs aligned for keyboard backlight applications. (Photo courtesy of Rohinni) |
LED die manipulation process
Rohinni came under the media limelight in 2014 for its paper thin LEDs made with 3D printing technology. The product was a prototype of its first generation micro-LED technology that could print red blood cell sized LEDs, which is about 9 micrometers, mixed with ink onto any substrate material.
Through trials and errors, the 3D printing technology proved uneconomic for commercialized production, but the experience laid the foundation of developing the second-generation technology, PiXey, which is fundamentally based on the high speed precise placement of micro-LEDs.
“We have developed an extremely rapid way to transfer micro LED’s to a variety of substrates that enables new design possibilities,” said the company CEO Matthew Gerber.
The company works with LED dies that are transferred by their own proprietary developed “Lumos” robot. The company uses existing fabs standard 6-inch wafers that are custom cut to even smaller than 100 microns.
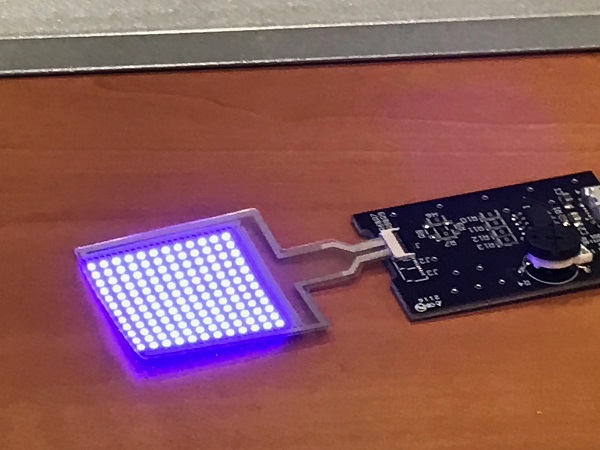 |
A close up of Rohinni's patented micro-LEDs for backlight applications. (LEDinside) |
The robot also uses Rohinnis proprietary intelligent algorithms to precisely place independent micro LEDs or groups of dies directly onto products.
“We can directly transfer Micro-LEDs through an automated process to eliminate packaging, sorting and binning, the result is perfectly uniform, bright, thin and extremely power efficient and much more cost effective light we call PiXey.” said Gerber.
The advantages of making micro-LEDs using individual component or unique component methods in the LEDs are single-head and can be tested independently. Asked how long it would take for the machine to sort micro-LED backlight for a notebook keyboard, Gerber said it would take 30 seconds.
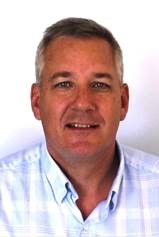 |
Brad Telin, Vice President of Operations at Rohinni. (Photo courtesy of Rohinni) |
“The process is even faster than today’s SMT and die sorting machines,” explained Brad Telin, Vice President of Operations at Rohinni.
Gerber declined to offer further details about the company’s micro-LED manufacturing process that places LEDs thinner than a strand of hair.
Clues of manipulating independent LED dies to make micro-LEDs can be found in Irish company InfiniLEDs publicized intellectual property, which explains forming light beams from LED dies without lenses. If Rohinni’s manufacturing process is similar to InfiniLEDs, to lower the micro-LED costs and raise lighting output, micromachining the surface of GaN wafers could leave parabolic mounds to control the dimensions means an LED junction remains on top of each mound, with the parabola focusing its light through the transparent wafer and out the other side.[1]
The actual manufacturing process might be different, but does shed light to potential technology possibility. Gerber said the company developed 36 patents with two additional fillings for specific applications.
The Idaho-based startup is ready to mass produce monochrome blue micro-LEDs for keyboard backlighting, and all other colors including RGB in Q1 of 2017.
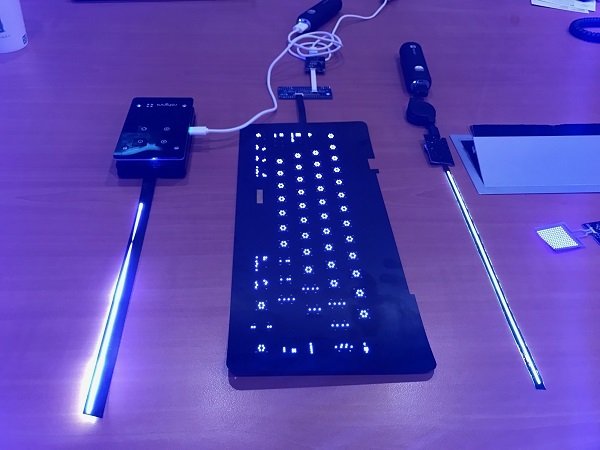 |
Rohinni's blue micro-LEDs strips and a sample of its micro-LED backlit keyboards. The photo was taken under a blue light illuminated room. (LEDinside) |
Rohinni micro-LEDs eyes industrial product design markets
Rohinni has targeted lighting applications in the industrial product design segment to offer computer, notebook, automotive and smartphone designers the ability to differentiate products with micro-LED light strips and logo designs.
The company formed a joint venture, Luumii, with Taiwanese keyboard membrane switch manufacturing specialist KoJa, to facilitate the mass production of micro-LED backlit keyboards that will be launched on the market by mid-2017.
“We decided to partner with KoJa because they are the best at what they do and the leading supplier of membrane switching in keyboards,” said Gerber.
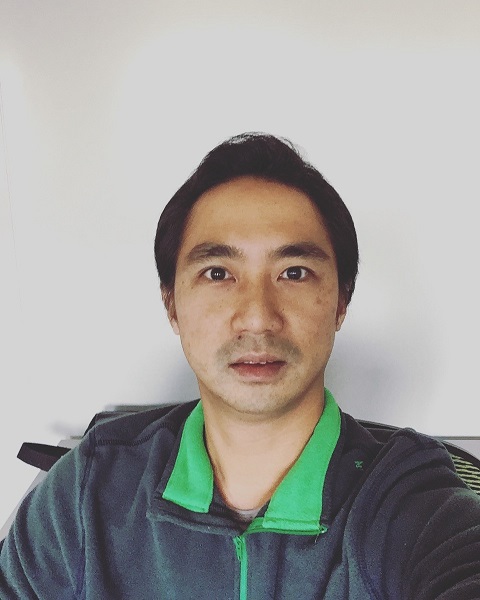 |
Kevin Lin, CEO of Luumii. |
“We have been negotiating an agreement over the last six months, and in talks for one year,” said Kevin Lin, CEO of Luumii.
The company is currently developing the high-volume manufacturing facility in Suzhou where they will produce the Micro-LED computer keyboard backlights.
Its micro-LED keyboard backlight products will be unveiled at CES 2017 in Las Vegas. Following the launch of keyboard backlight products, the next phase will involve LCD display backlight products that will keep the company busy throughout 2017, while mobile and wearable applications will not be launched on the market till after 2018.
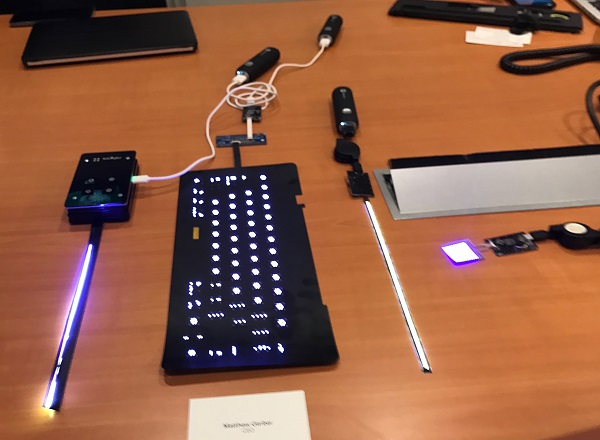 |
Samples of Rohinni's micro-LED products including light strips, keyboard backlight, and LEDs viewed under normal lighting .The LED light strips can be programmed to flash in different patterns and even colors using appropriate LED controls. (LEDinside) |
For smartphone applications, Rohinni is targeting mostly an aesthetic approach that can help smartphone makers differentiate their products with more distinctive indicator lighting and fingerprint recognition lighting.
Gerber estimated combined the notebook, tablet, smartphone and wearable market values US $4.33 billion, while automotive lighting approximated US $1.4 billion in 2016.
In the automotive lighting sector, Rohinni will be applying its micro-LEDs in car logos, interior decorative lighting, accent lighting, taillights and decorative lighting, with an estimated release date in late 2017.
In the meantime, Luumii (The Rohinni/KoJa joint venture) is working hard with keyboard manufacturers to offer the world’s thinnest, brightest and most power efficient backlighting systems for laptop use.
Reference
[1] http://www.electronicsweekly.com/news/business/finance/infiniled-micro-led-start-up-2013-05/